So I decided to make my own.
This only cost me about $50 in materials and I had a few things lying around, as did my dad.
This is basically as it sits without the top clamping piece. It's two lengths of 10mm (i think) angle iron, they have been notched out for clearances (where the hinges are) and two hinges made (using a pin and a sleeve). 1 half of the hinge is welded to one bit, and the other to the other bit of angle.
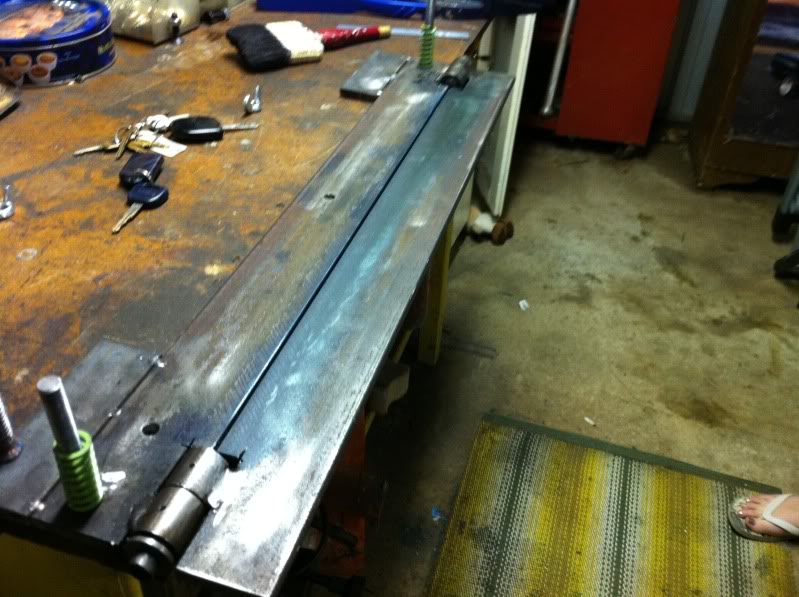
This is a closer look at the hinges. You would also notice the long threaded bolt with the spring. The top bit of angle that clamps onto the sheet metal is drilled out so it can slide up and down the threaded bolt. The spring is there to help you lift it back up once you undo the wingnuts.
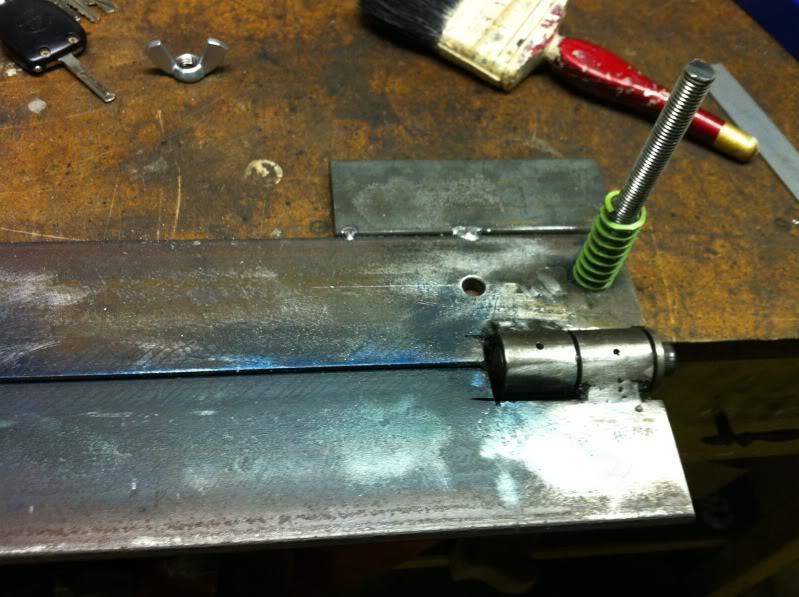
As you can see, the part that isn't bolted onto the edge of the table can easily be lifted up and can bend over 90 degrees.
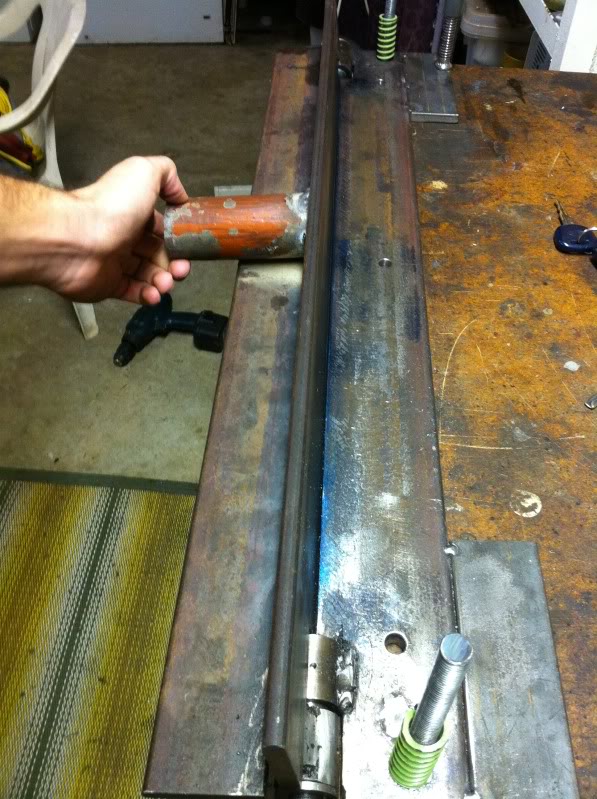
Another look at the hinge. The holes are just a lubricating access point or something haha
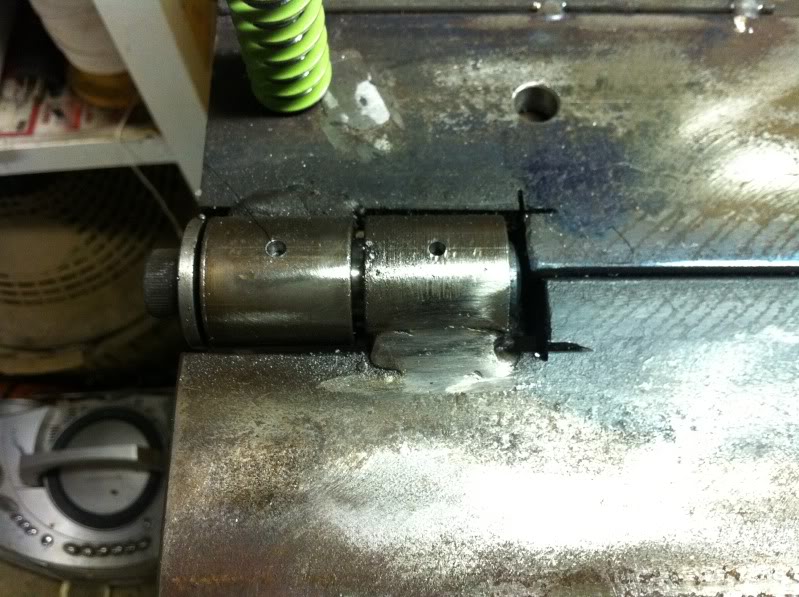
This is where a pole can slide into the sleeve so you can get as much leverage as you like (the longer the pole the better leverage obviously)
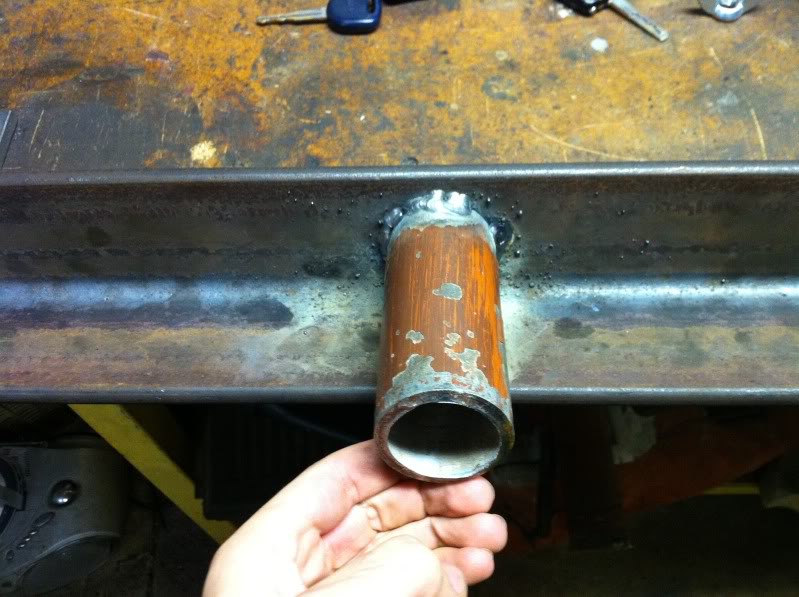
This is the top clamping piece of the brake. The top edge was grinded flat so a hole can be drilled so the threaded bolt can go through.
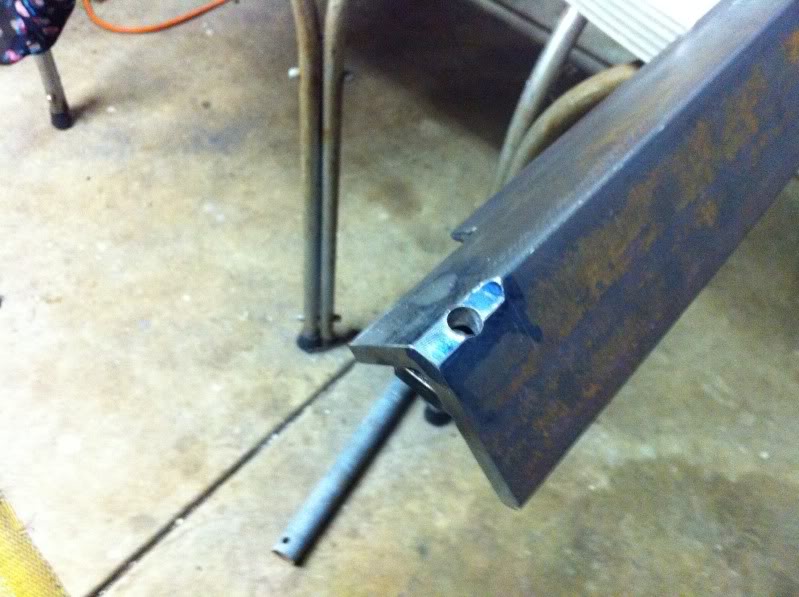
The edge on the left was grounded flat for more crisper bends
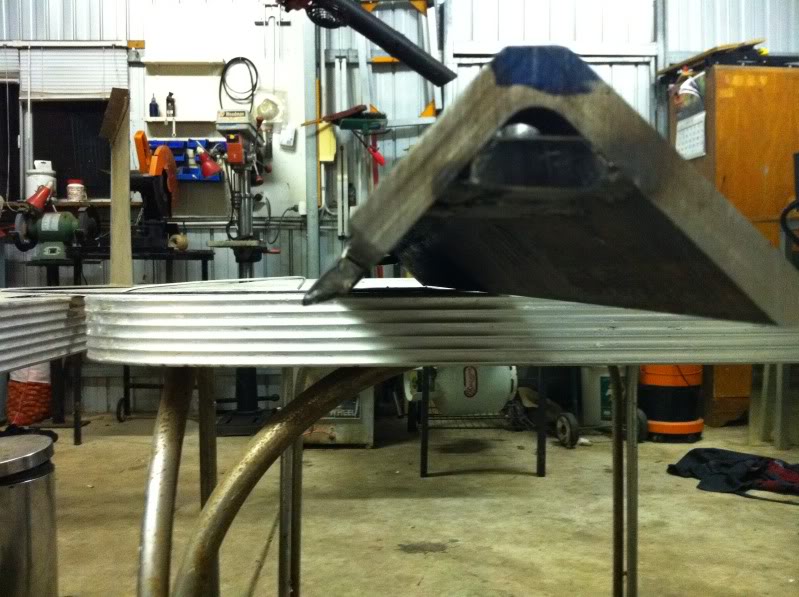
You can see where a little bit of steel was welded in there for the spring to sit straight
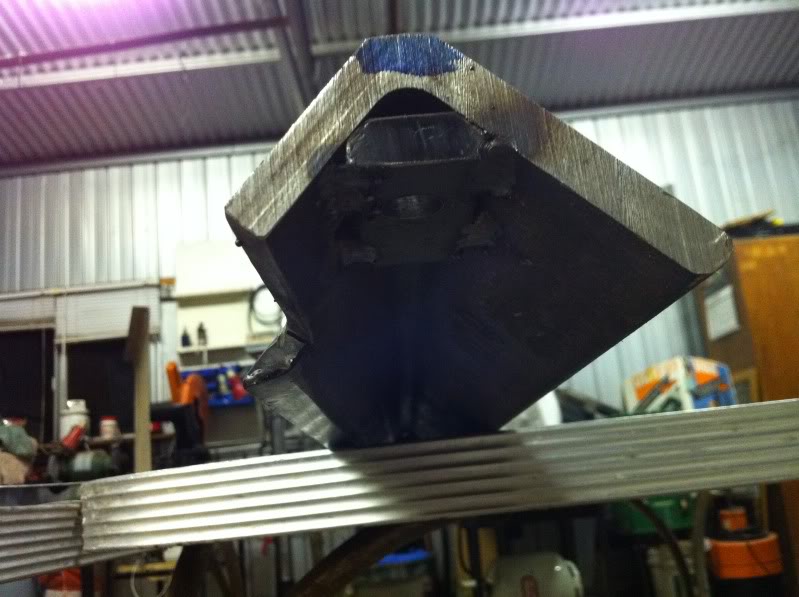
There is basically the whole unit. Spring holds it up, slide sheet metal in...
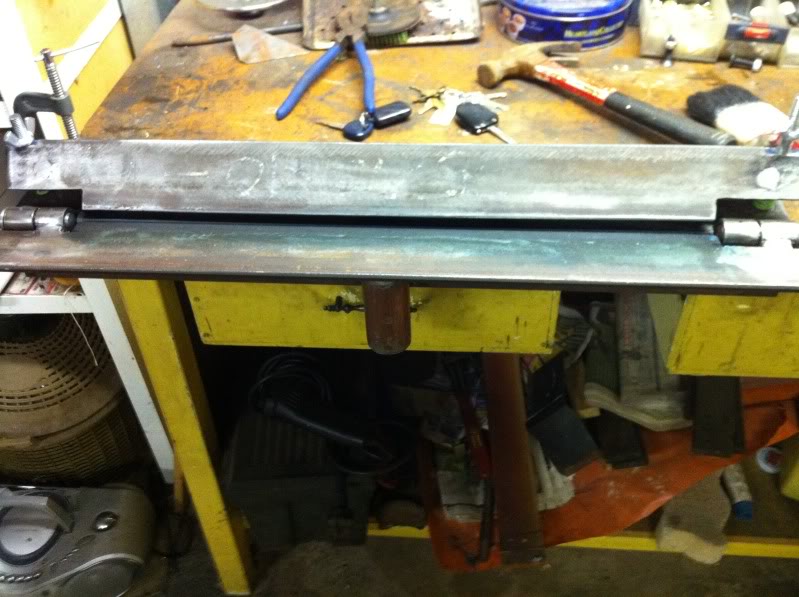
This is me pushing the clamping section down, screw the wingnuts down for a nice clamping effect. (much better than using g clamps)
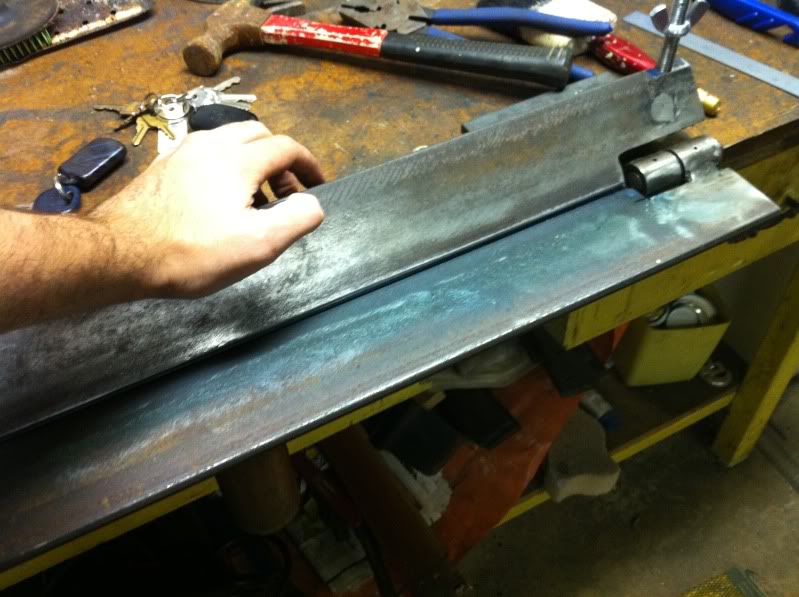
Trial bend with some galv
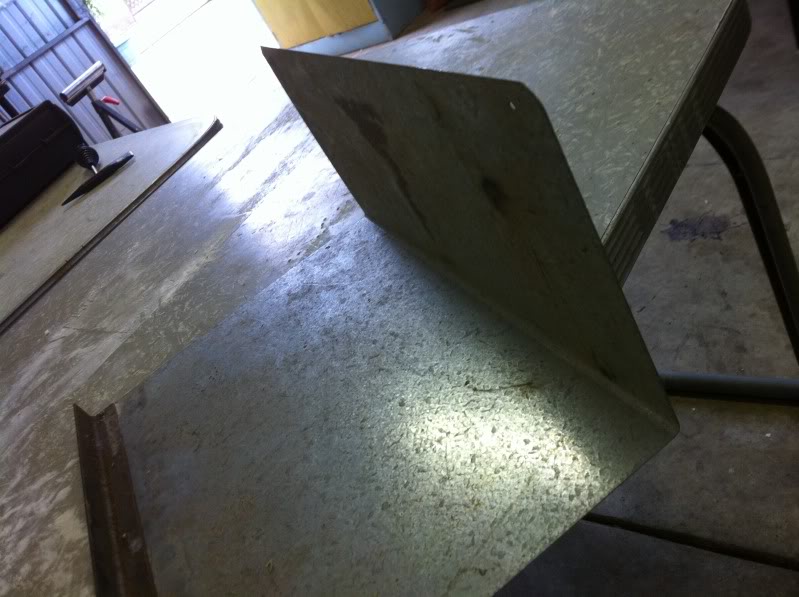
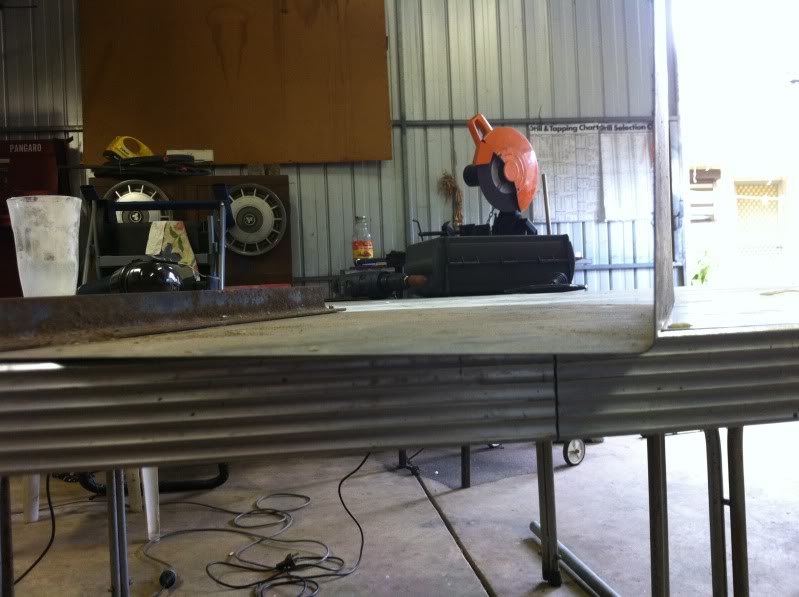
and this is after I bent some 2.5 mm steel
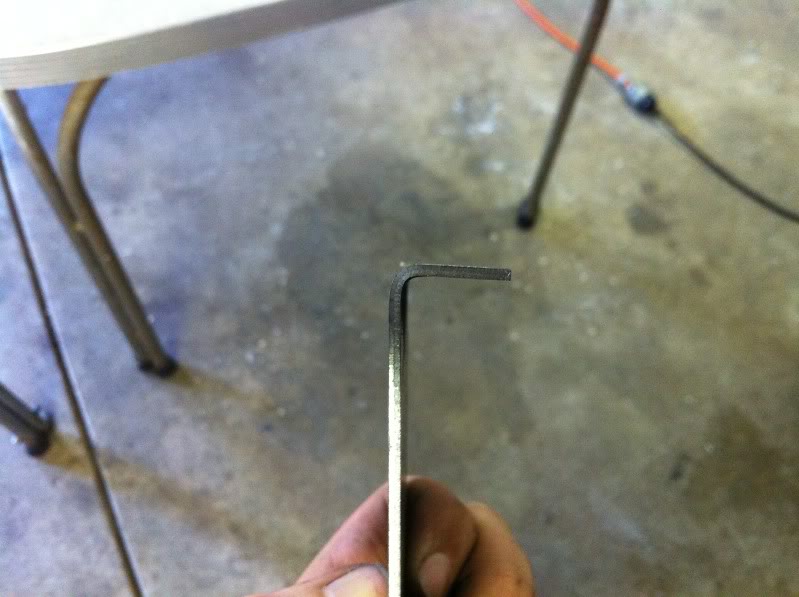
Look for how much it cost, and the time it took to make, it does what I want for a smidgen of the price. only 99% complete, I just have to bolt it to my bench give it a lick of paint or something.
Thanks for letting me share