Material required:
*Template cardboard (A3 cardboard from newsagents)
*Sheet metal
*MIG Welder.
This is what I was trying to replicate...
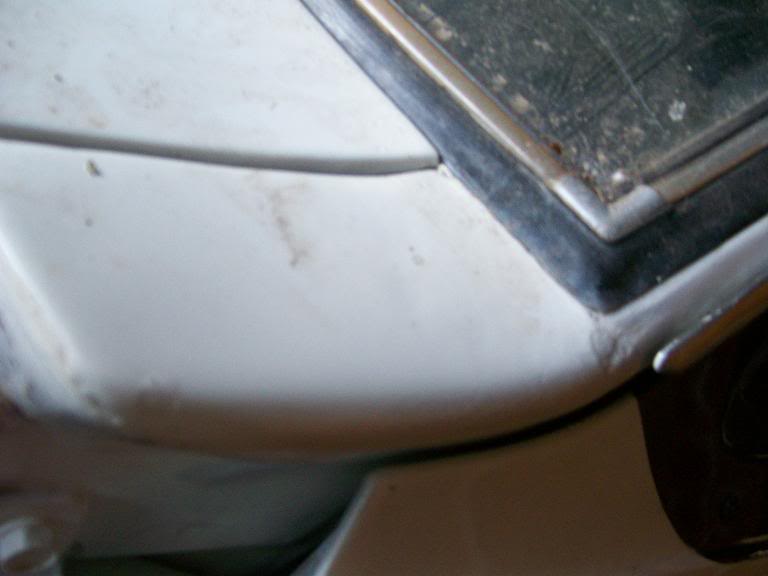
Ok first up I had to make a template for the top face.
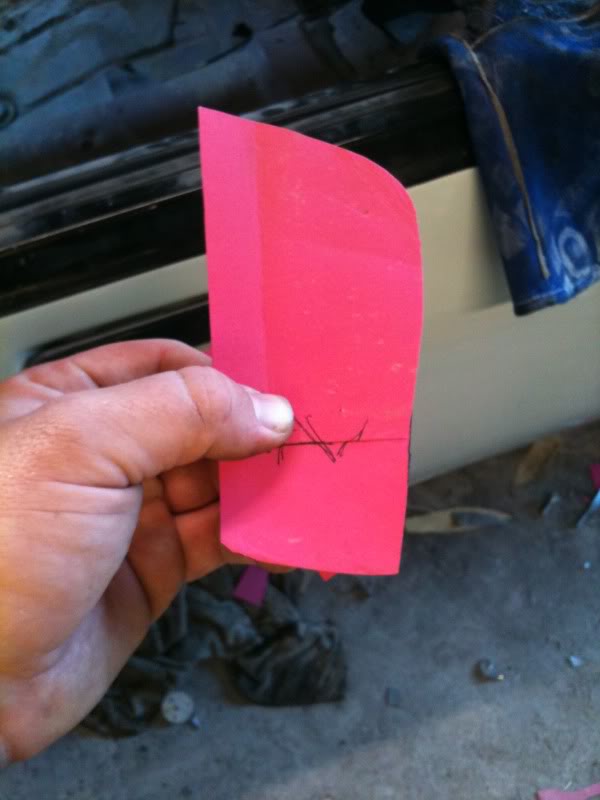
I didnt bother putting a side on it because both my sides are different from me fabricating the pillar itself. BUT put this section on, so the once cut out of the metal you can just run it as a sharp joint, the gentky radius it around til you get the shape you want, hopefully same shape as guard. (I had already tacked mine up before pics sorry)
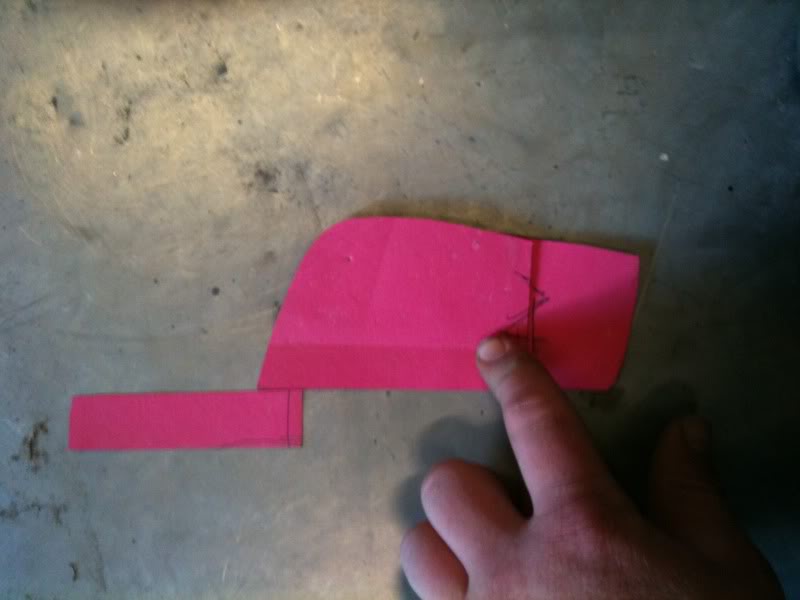
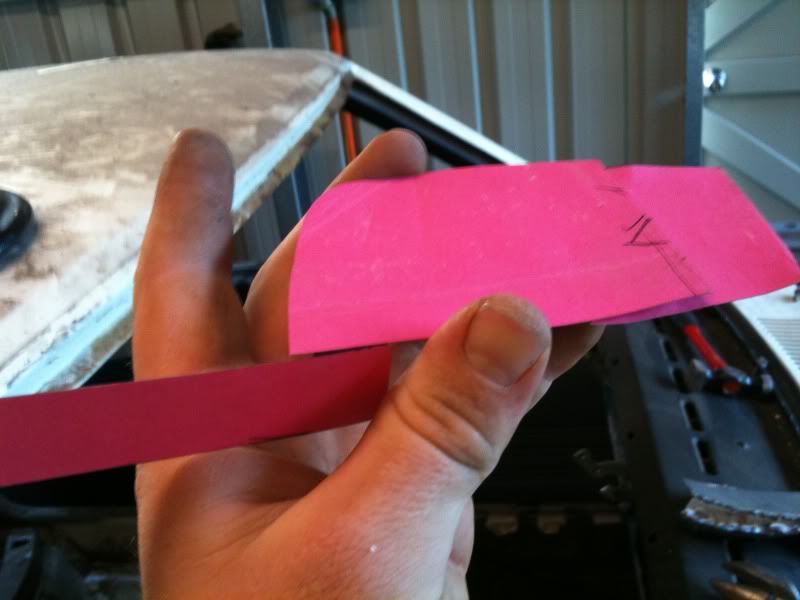
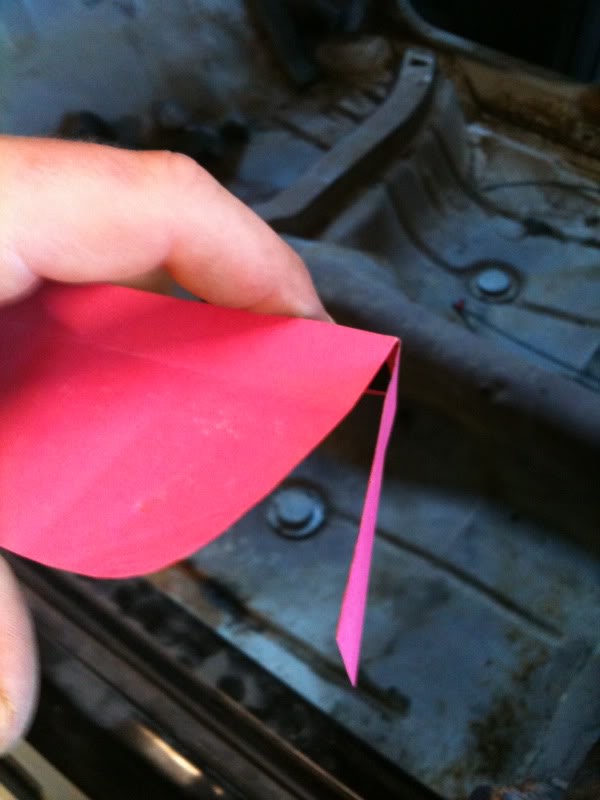
Tacked on. Notice the gap is pretty constant.
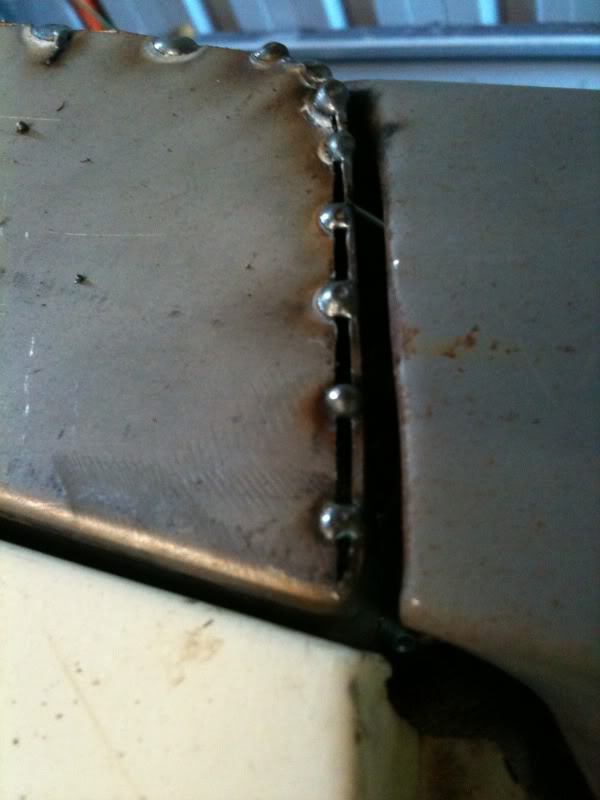
Now cut out a little template to run along one side by holding cardboard flat on pillar and marking the contour of the plenum cover, cut out of metal and tack it on.
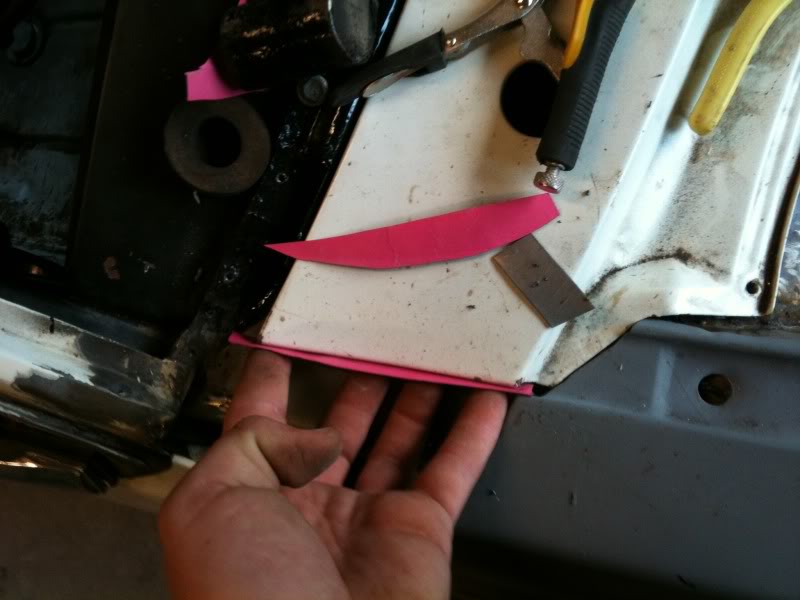
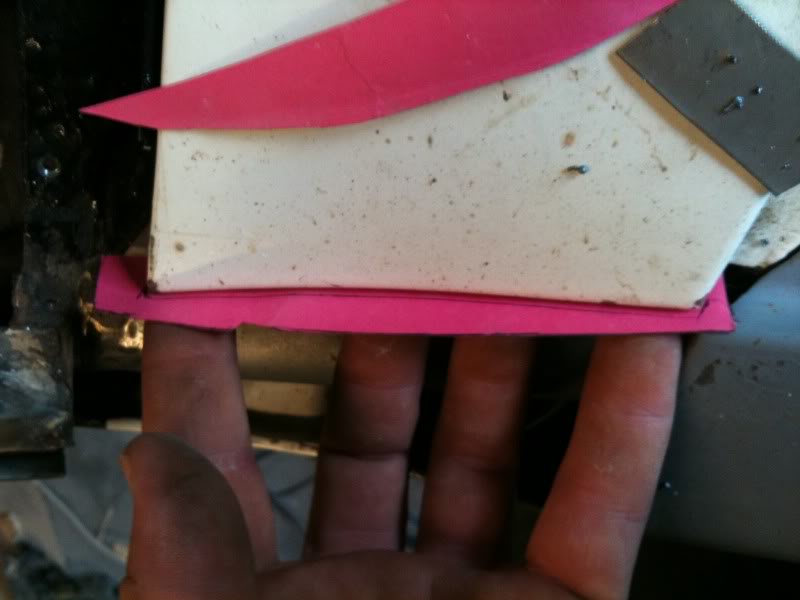
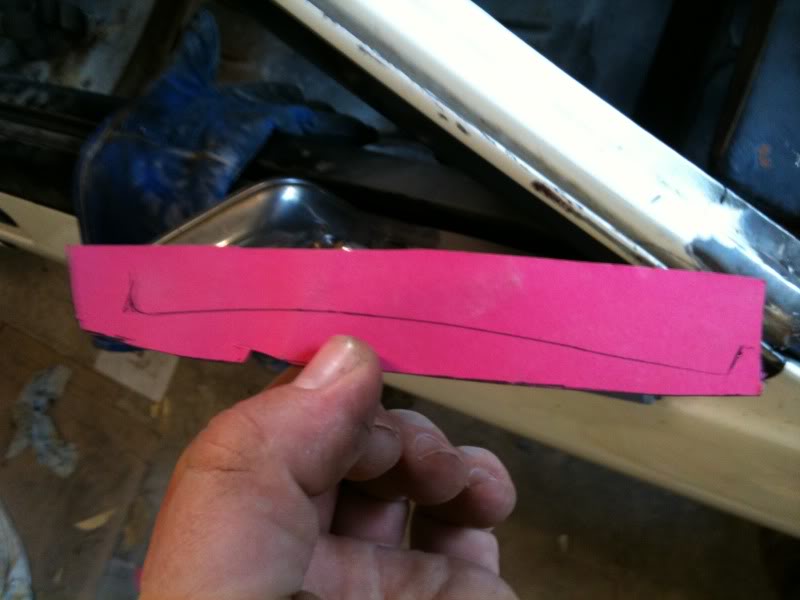
Now once that is done you can form the top piece how you want and tack it place (temporarily).
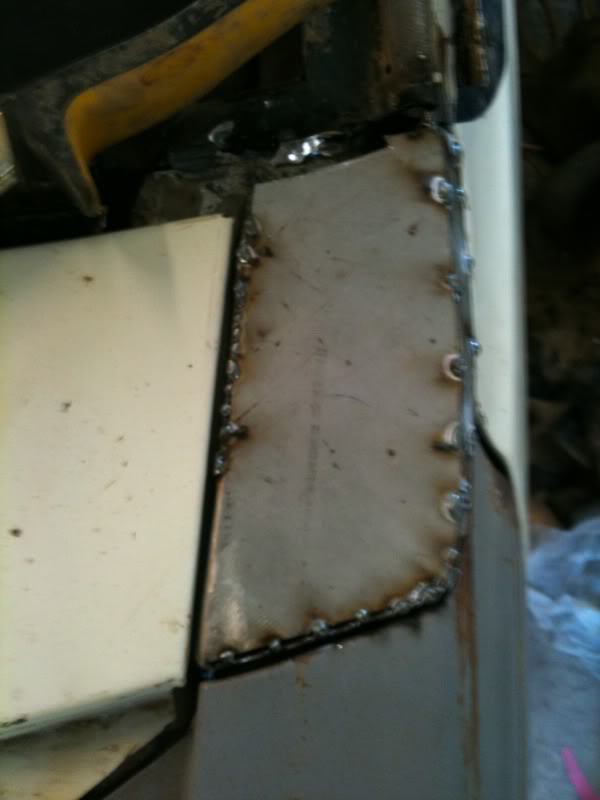
Make a template for the outward facing side making sure you have an even gap all the way. Cut it out, tack it on again.
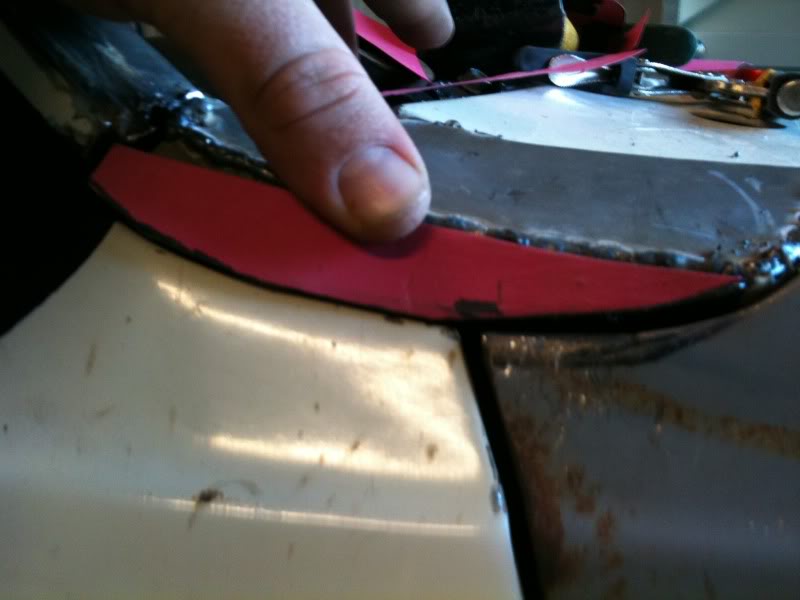
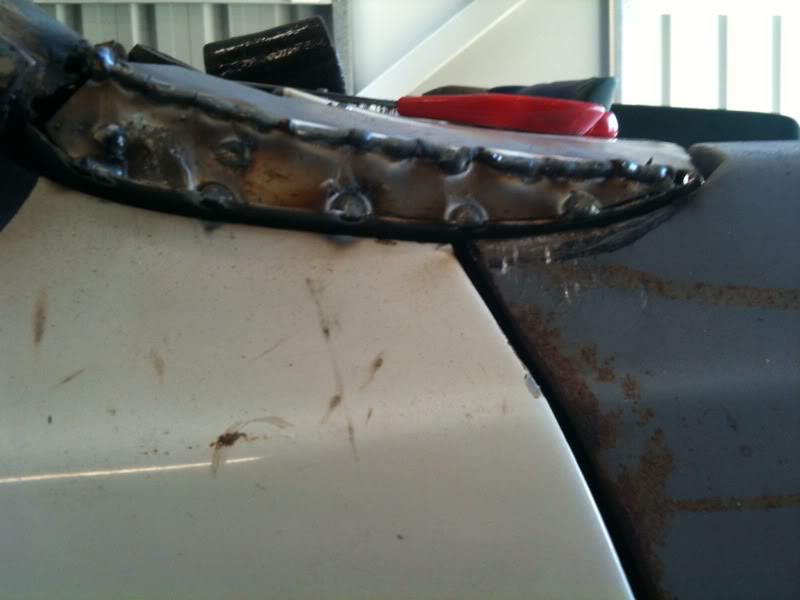
Last piece is basically piece of cardboard shoved underneath and marked and the cut out and tacked on making sure shape is as close as possible to guard and door.
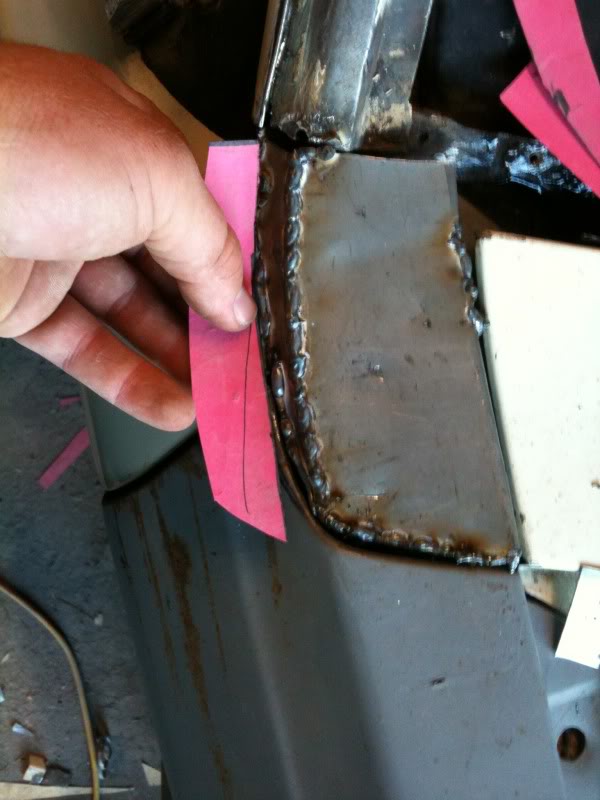
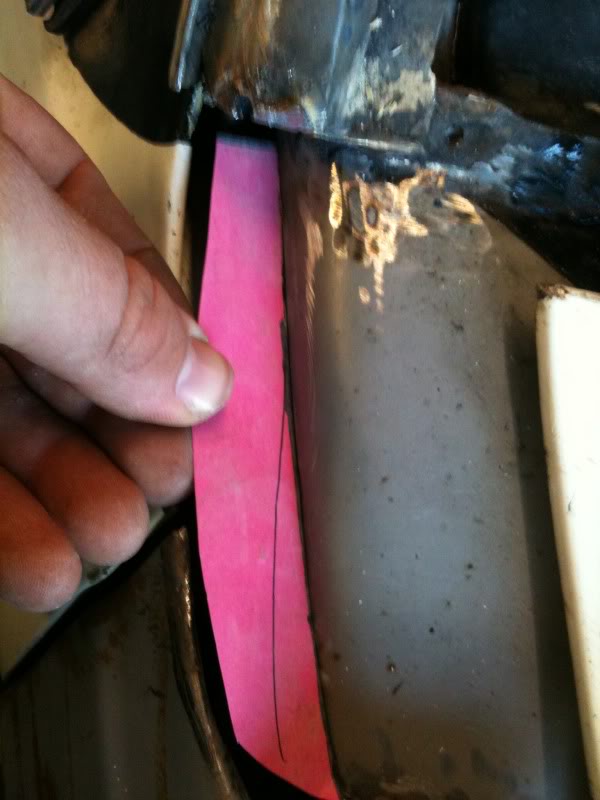
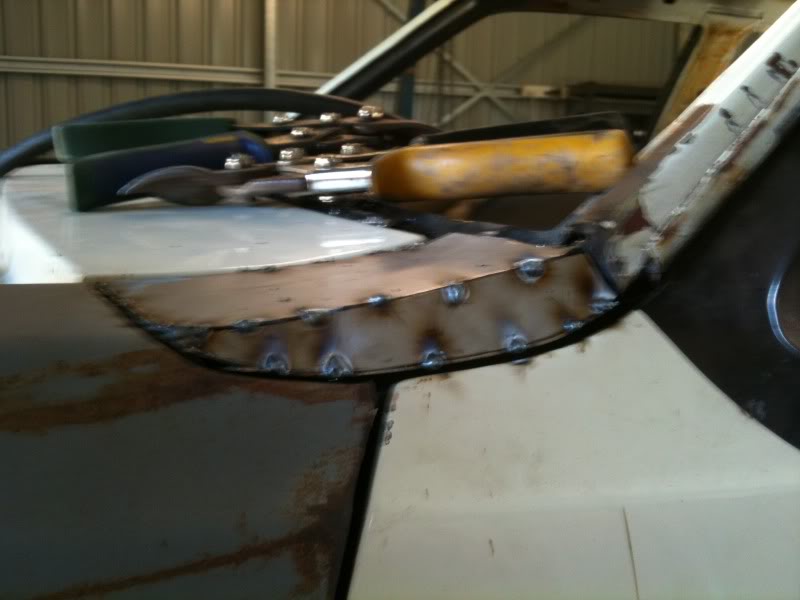
Now once thats done, weld it all up.
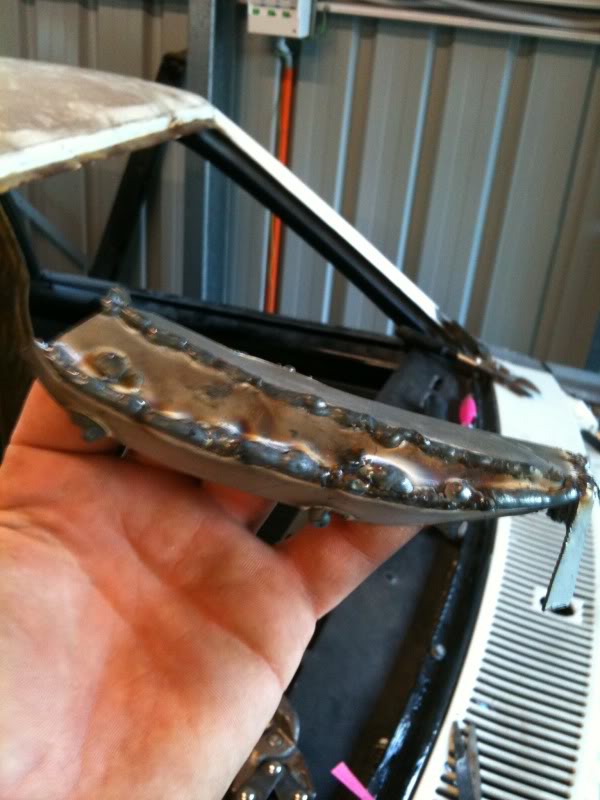
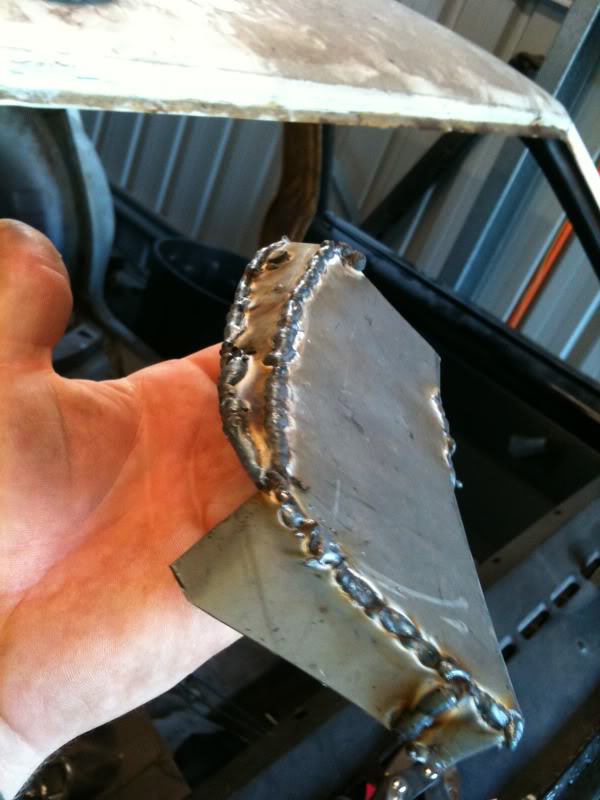
Grind it smooth and cut out the water drains (which I havn't done yet, will post up picture of completed product in the next couple days.
Here's a couple of pictures with it all tacked up ready to weld.
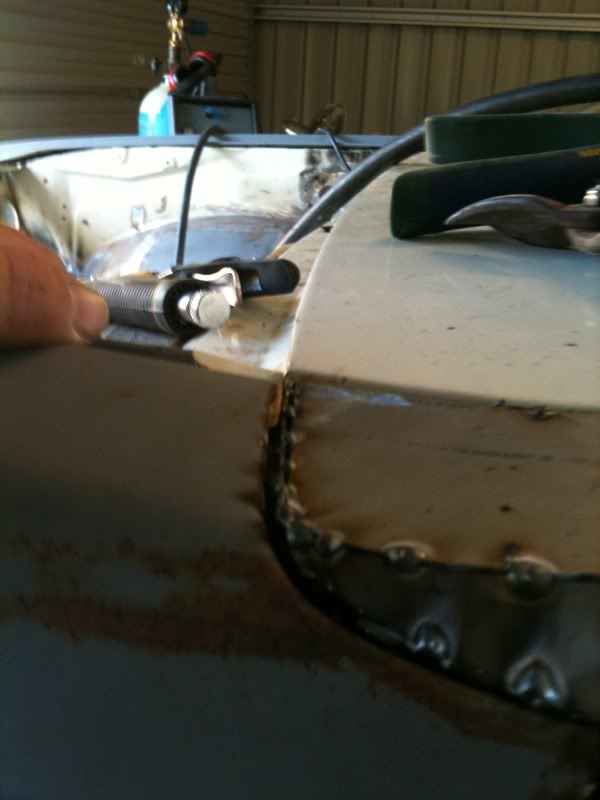
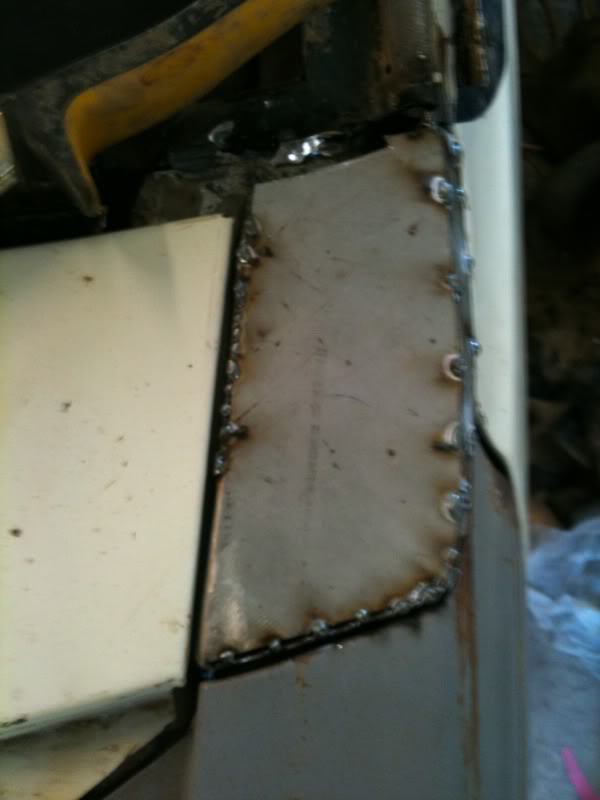
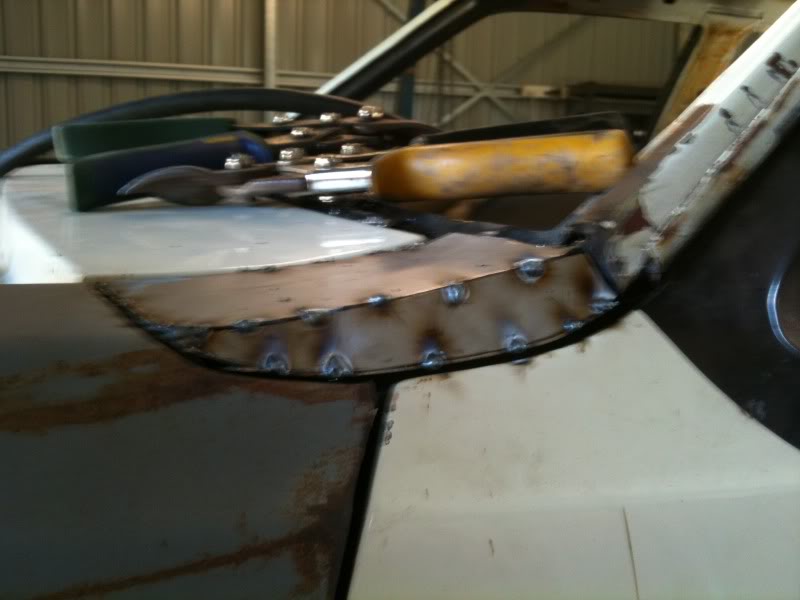
But that's basically all there is to it... I'll put some more pics up when I'm done but you get the picture... I hope.