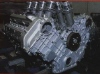
Titanium Tubular control arms
#1
Posted 15 April 2006 - 01:38 PM
My biggest concern is what wall thickness to use to make a titanium tube control arm and what grade of titanium.
The best information i recieved was from a bloke in England who was making titanium control arms for a mini, which is significantly different to an LJ or LH/X/UC, in length and weight of the car, although he did use grade2 titanium.
#2
_CHOPPER_
Posted 15 April 2006 - 05:16 PM
#3
Posted 15 April 2006 - 07:39 PM
#4
_conceptss_
Posted 16 April 2006 - 09:18 AM
http://www.azom.com/...razing_Titanium
http://search.ebay.c...bjss1975QQhtZ-1
#5
Posted 16 April 2006 - 01:37 PM
The titanium the English bloke used was grade2 which could be why he doesn�t stress relieve his components.
Unfortunately his website doesn�t come up anymore
I have found a couple of titanium welders in Sydney but I haven�t spoken to them yet as I don�t have any titanium arms to weld yet.
I wonder if toranamat69 has found anything in regards to this.
I have seen titanium tube approx 14inches long, 1.25inch dia with 1.3mm wall go for about $40Au.
I was tempted to buy approx 6 peices but wasnt sure on the wall thickness and grade being right.
Edited by Bart, 16 April 2006 - 01:44 PM.
#6
Posted 16 April 2006 - 01:45 PM
What I do remember is you are quite limited in the actual tubing sizes available in Ti.
Since I still didn;t know what shape and how the control arms will eventually look in tubular version, I have taken the choice of doing the development work on mine in steel and then upgrading later when I have a proven design. The Ti tubing was bloody expensive to be chopping up and throwing away dead bits.
My compliance engineer was not too worried by the prospect, just requiring I prove the strength of the tubing by calculation and having everything welded in accordance with the Australian standard.
The welders at the place I used to work were very proficient at Ti welding and there are a few special considerations you had to take into account but nothing really speciallised required to do the job.
You had to back purge the weld with shielding gas as well as the normal shielding gas on the face of the weld. You require an AC Tig as you need for alloy welding, the correct filler rod for the grade you are welding and don't try to weld any other types of metals to it as it doesn't work.
One of the best sources of threaded rod adaptors and Ti tube was a racing crowd I found in the US but I don;t have the link anymore.
Basically at the end of the day I concluded there are about 100 other things that make Toranas handle like crap other than the heavy unsprung weight.
Still something I may eventually do - on the rear lower arms first though as that would be relatively easy.
M@
#7
Posted 16 April 2006 - 08:22 PM
So there you go Concept SS was onto it.
A speciallist should be able to do this for you as mentioned.
M@
#8
Posted 17 April 2006 - 01:50 AM
I mean are they fairly common or rare and specialised with military??
#9
Posted 17 April 2006 - 09:38 AM
#10
_82911_
Posted 17 April 2006 - 03:08 PM
The guy who refines my scrap metals for me (platinum/palladium and AU) and who is a very accomplished and published metalurgist has assured me in the past that there is no way to succesfully weld Ti outside of a totally inert chamber.
He and I have had this disscussion on many occasions, as I am constantly searching for a way to joint Ti other than riveting.This is for Jewellery making by the way... hardly stuctural I know, but he tells me the results will be the same... SNAP!
Cheers Greg..
#11
_JBM_
Posted 17 April 2006 - 04:24 PM
Once you have a pattern you can make as many as you want in whatever material you decide to pour in.
James
#12
Posted 18 April 2006 - 03:31 PM
They might be willing a lend a jig?? Worth a shot.
Grant..
#13
Posted 19 April 2006 - 11:11 PM
titanium does not if welded properly ie in a chamber.
i dont think TSS will lend much at all let alone a jig unfortunatly.
I will find out more about this inert gas thingy



Edited by Bart, 19 April 2006 - 11:17 PM.
0 user(s) are reading this topic
0 members, 0 guests, 0 anonymous users