Cool.
Black spots = contamination.Probably oil.
Clean everything spotless with clean rags and acetone before welding.
I would use more tacks closer together.You can file or grind the tops off the tacks before you fully weld the joint to prvent those lumps when you weld back over the top of them.
If you are filing things before you weld,try and keep a set of files to use only on ally,you can contaminate your joints very easily with ally.Same thing with grinding wheels,use a fresh one and keep it for ally.
A tip when welding a box and you are welding towards a corner,start at the far corner and weld back about an inch.Then start at the other end and weld towards the corner you just welded.
That way you can finish the weld before you get to the corner where heat has a tendency to build up and cause material to drop away.
I hope that makes sense.
Looks pretty good so far for a guy with limited experience.
Keep practicing .

Tig Welder Settings
Started by
_Viper_
, Jul 25 2011 04:54 PM
33 replies to this topic
#26
Posted 06 August 2011 - 11:06 PM
#27
_tomo123_
Posted 08 August 2011 - 02:57 PM
Looks good viper,
i use brake clean to clean my joints before i start welding as opposed to acetone
i use brake clean to clean my joints before i start welding as opposed to acetone
#28
_Viper_
Posted 08 August 2011 - 09:20 PM
Thanks for the tips wot179 and tomo, I welded in the 3" pipe inlet today... Internal corners (T joint whatever it's called) are heaps harder... Had trouble aiming the puddle sometimes it would sit on the base peice and not want to go up the wall (sorry I don't know the proper terms)
Should I be using a thinner tungsten for thinner material? Or is it one size fits all?
Does anyone know a link for a pic showing the angle you should hold the torch at for each joint type?
Should I be using a thinner tungsten for thinner material? Or is it one size fits all?
Does anyone know a link for a pic showing the angle you should hold the torch at for each joint type?
#29
_Viper_
Posted 08 August 2011 - 10:19 PM
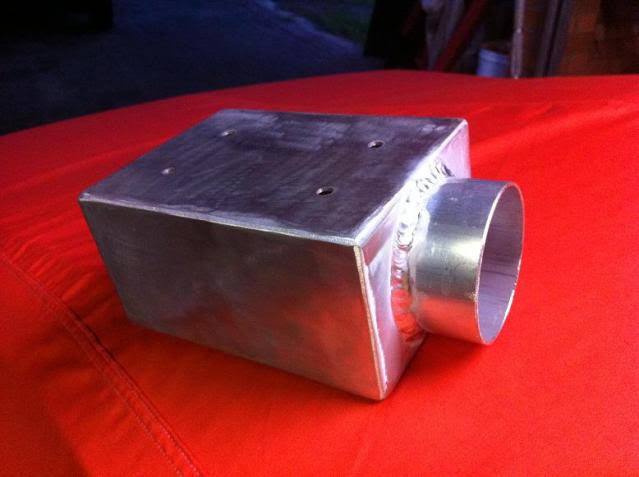
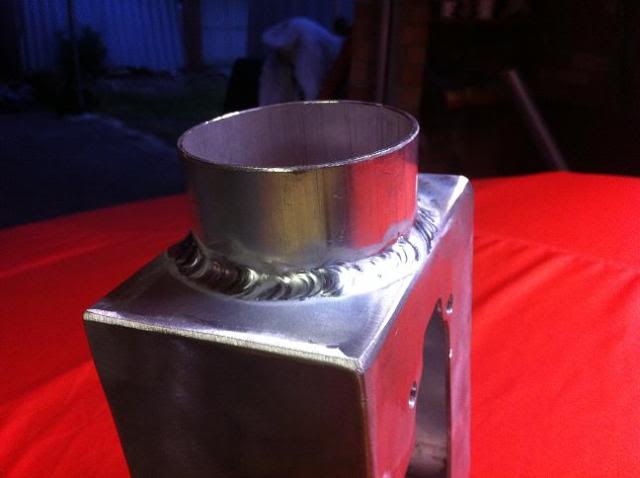
Thats the sort of joint im talking about? would you call that a "internal corner" ? whats the best angle to hold the torch at? I also found that I needed to use the thicker filler wire as well as more amps?
#30
_1uzbt1_
Posted 09 August 2011 - 10:07 AM
I've had trouble doing the same joins, most people have said you need more amps. Your suppose to hold the hand peice at a 45 degree angle when doing a 90 degree corner fillet.
#31
_tomo123_
Posted 12 August 2011 - 03:11 PM
viper this may not be 100% correct but this is how i do fillet welds and it works for me
hav your tungsten out about 6-8mm
aim the tungsten directly into the corner at 45 degrees
when you get a weld pool going add your filler wire to the top edge, it generally rolls down and will fill the vertical and horizontal piece
hav your tungsten out about 6-8mm
aim the tungsten directly into the corner at 45 degrees
when you get a weld pool going add your filler wire to the top edge, it generally rolls down and will fill the vertical and horizontal piece
#32
_Viper_
Posted 12 August 2011 - 05:29 PM
Cheers for the tips. Got a new issue.
Was welding some mild steel today and it was going sweet then every now and then you could see the weld pool look as tho It was boiling and when you stopped all air bubbles formed... Looked like it does when I use the mig and forget to turn the gas on.
But I has the gas on and flow rate was 15, tried upping it to 20.
I was using straight argon, would that be the cause? Should I be using Argoshield?
Was welding some mild steel today and it was going sweet then every now and then you could see the weld pool look as tho It was boiling and when you stopped all air bubbles formed... Looked like it does when I use the mig and forget to turn the gas on.
But I has the gas on and flow rate was 15, tried upping it to 20.
I was using straight argon, would that be the cause? Should I be using Argoshield?
#33
Posted 15 August 2011 - 10:29 PM
My straight argon with carbon steel works fine. Those air bubbles are called porosity.
I would say that it is contamination in or on the steel causing it to flare up or wind blowing the gas away.
Make sure there is no wind. I only usually use about 7 on my gas.
Nice work on those projects. They look very professional.
Ev
I would say that it is contamination in or on the steel causing it to flare up or wind blowing the gas away.
Make sure there is no wind. I only usually use about 7 on my gas.
Nice work on those projects. They look very professional.
Ev
#34
_Viper_
Posted 16 August 2011 - 08:24 AM
Nice work on those projects. They look very professional.
Only cos I ground all the bad welds smooth haha. but thx
Yea I did some more steel on the weekend and it was perfect :S so possibly just wind... I did eat baked beans that day

1 user(s) are reading this topic
0 members, 1 guests, 0 anonymous users