I have a similar thread on another forums so ill just steal a few pics of stuff I done in the past first...
My work bench
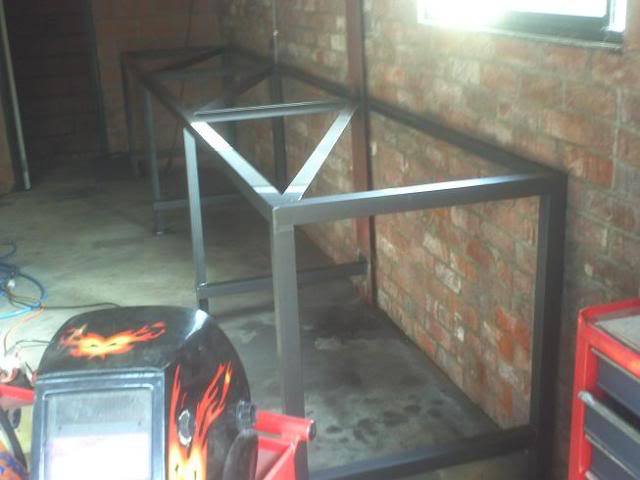
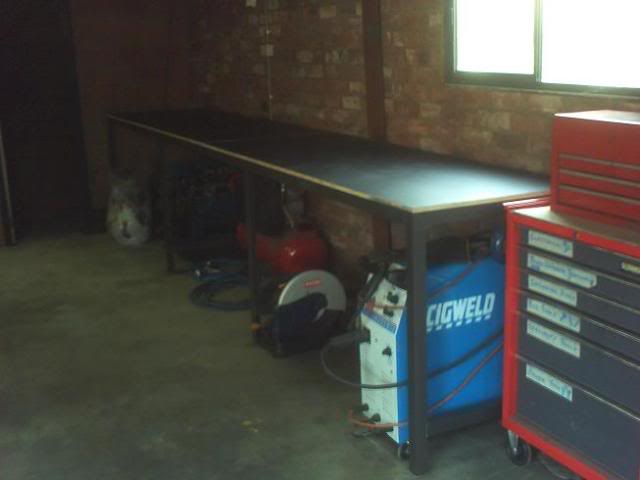
Bunch of brackets I made for people to mount gas struts for there bonnet into Gemini's
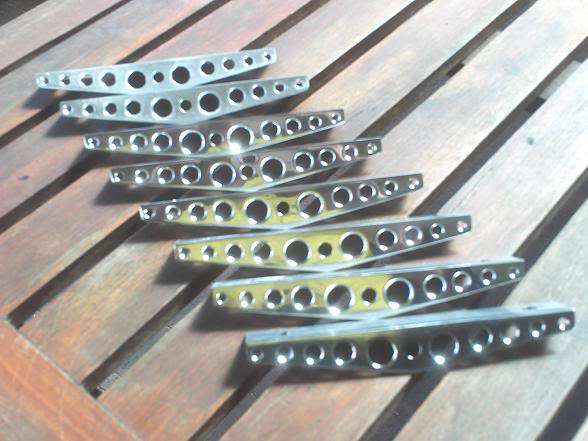

little carby box... The guy wanted a rectangle shape

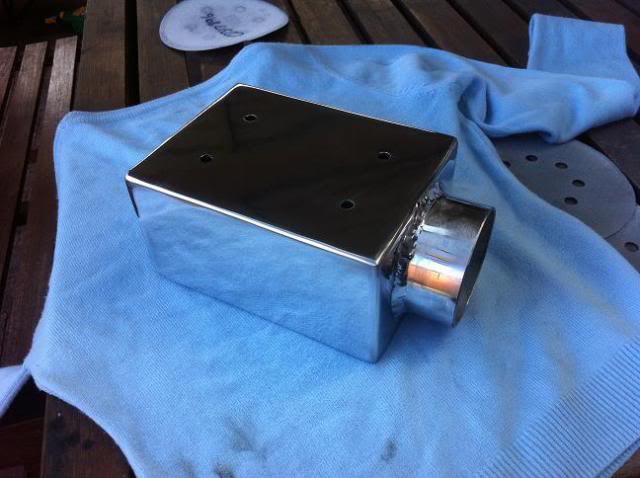
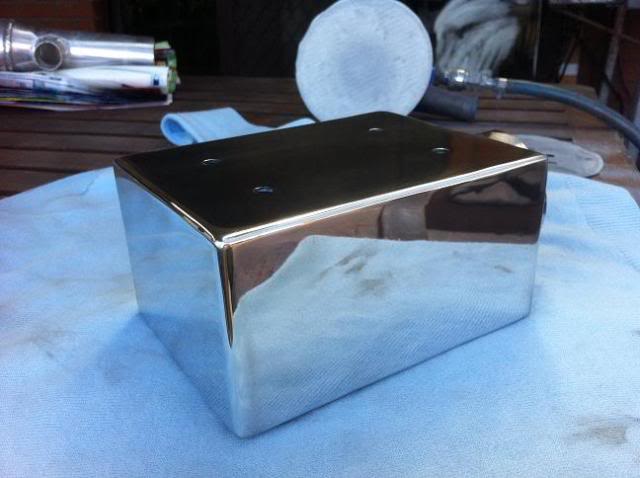
Some seat rail adapters for aftermarket seats into Gemini
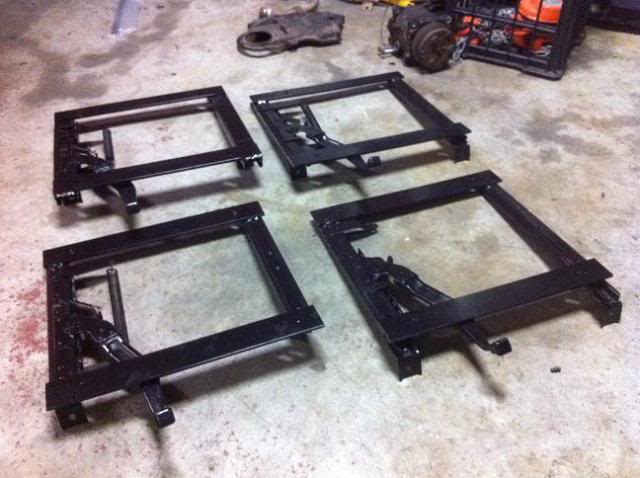
3" Mandrel exhaust for my Turbo coupe


Accelerator cable bracket (would usually just weld a tab onto the plenum but he already had it painted)
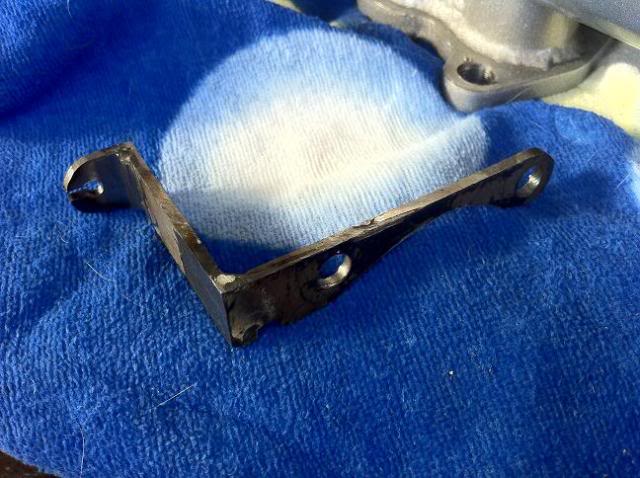
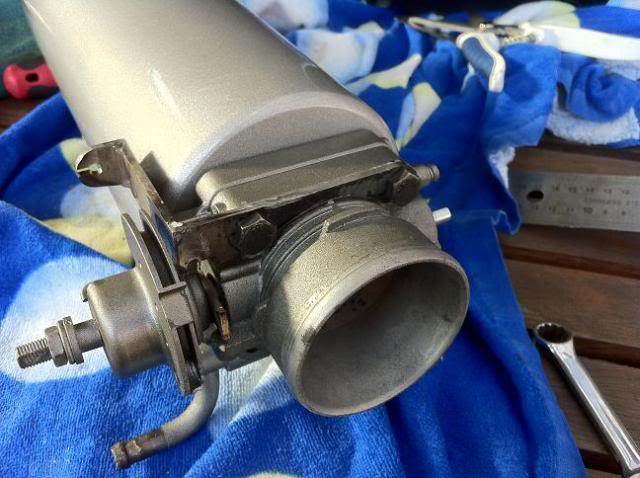
Some work I did for a guy with a V6 Turbo Gem with 500rwhp
Oil Feed and drain fitting
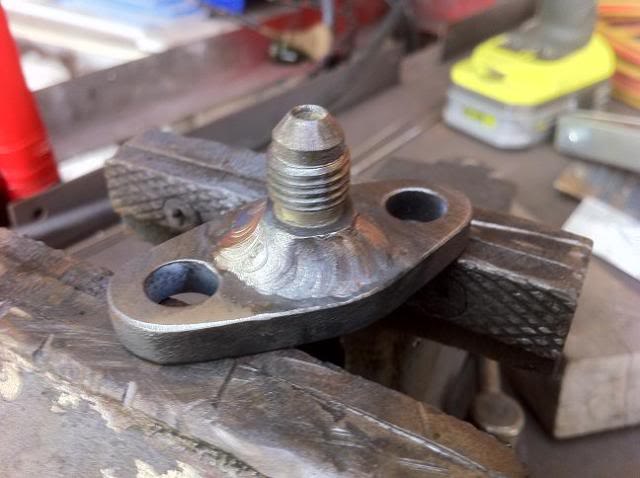
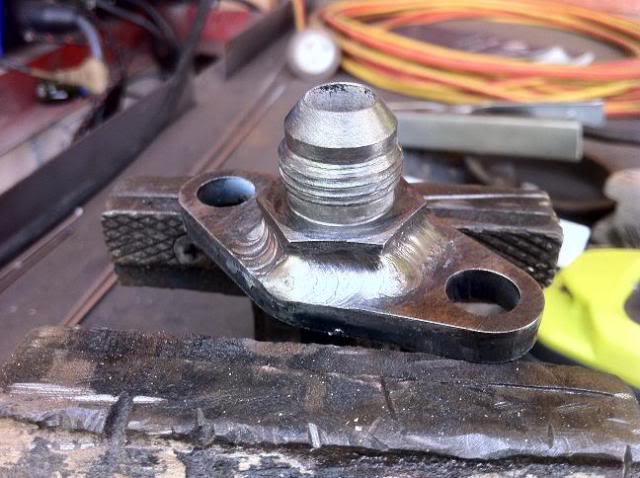
Exhaust
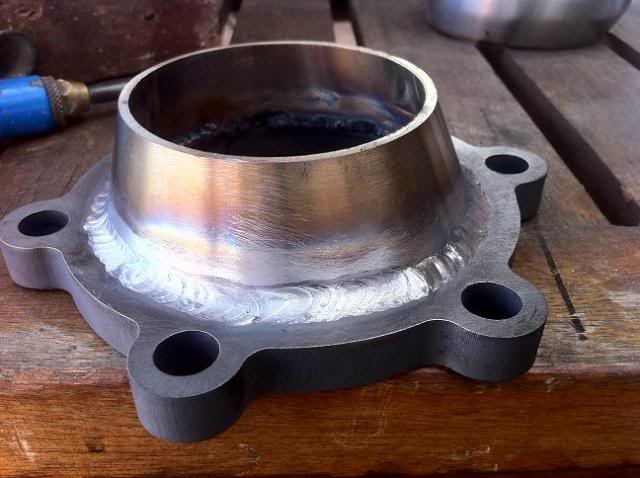
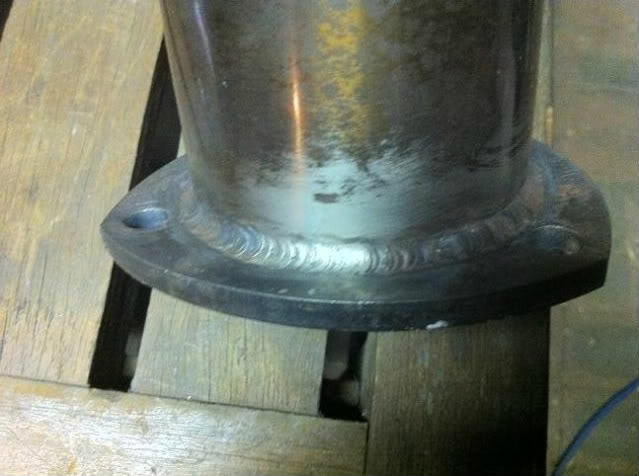
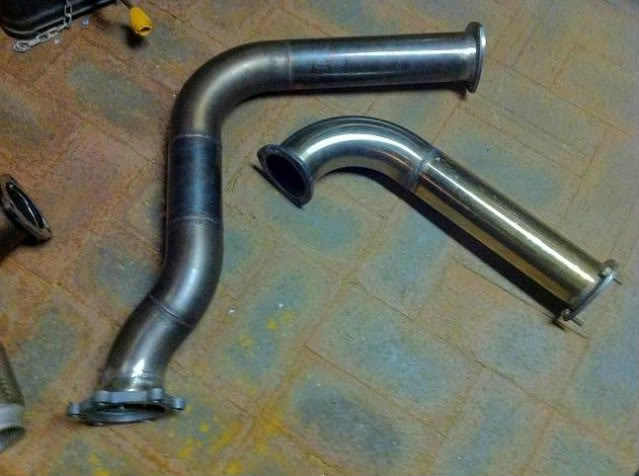
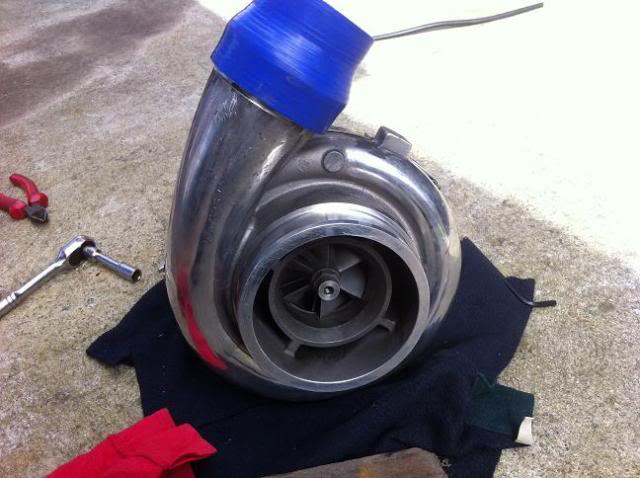
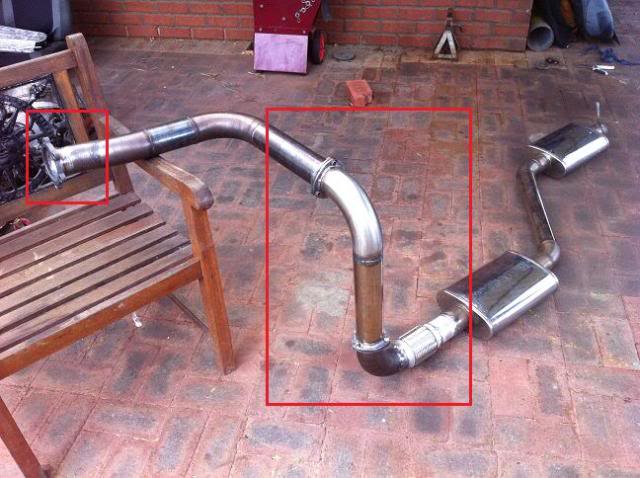
Engine I recently built, is in his car and running now, just did the 200km oil change yesterday
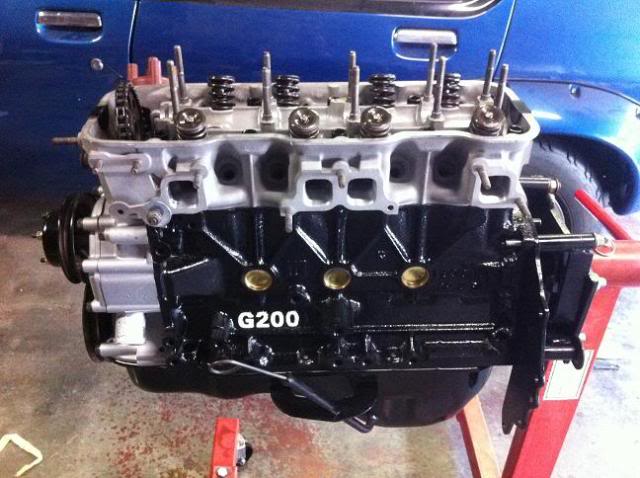
13B Rotary into Gemini
Engine crossmember
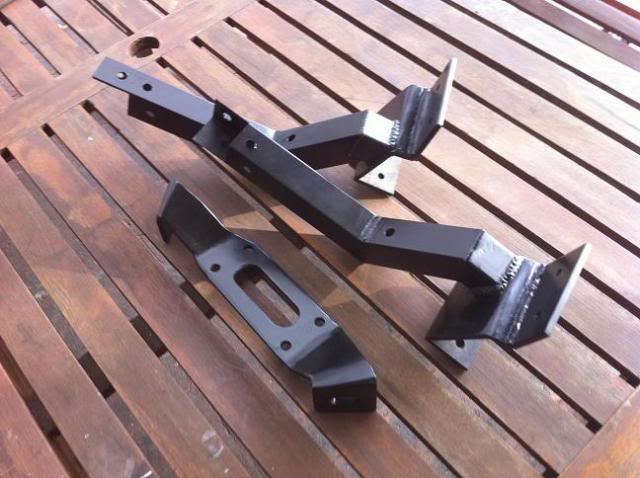
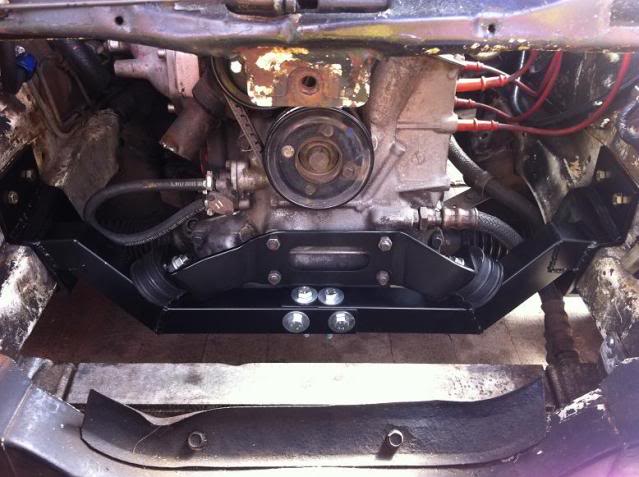
Clutch cable bracket
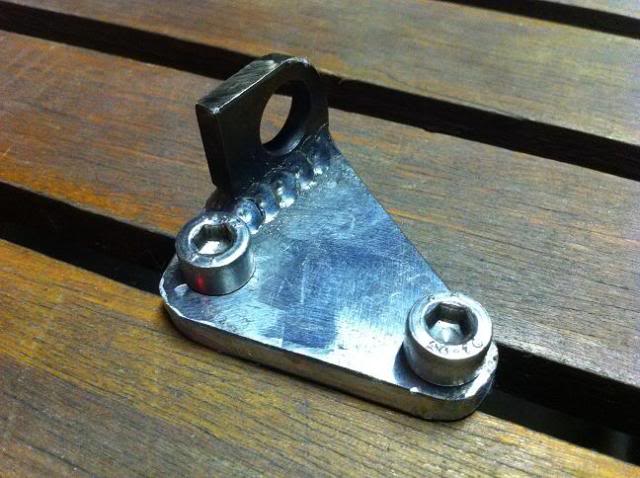
Cut, rotate and re-weld rad pipe
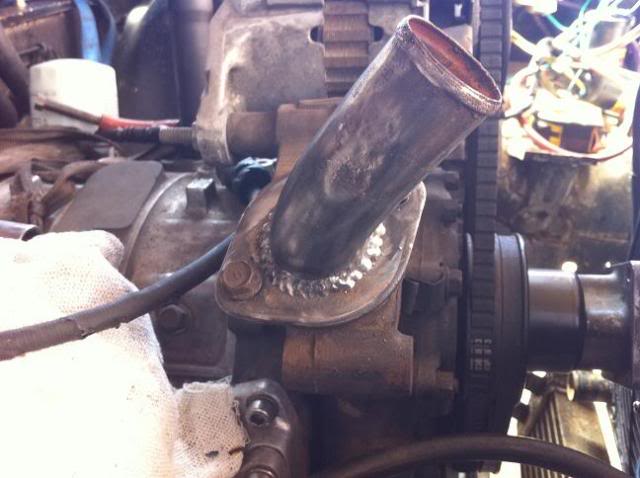
Accel cable bracket
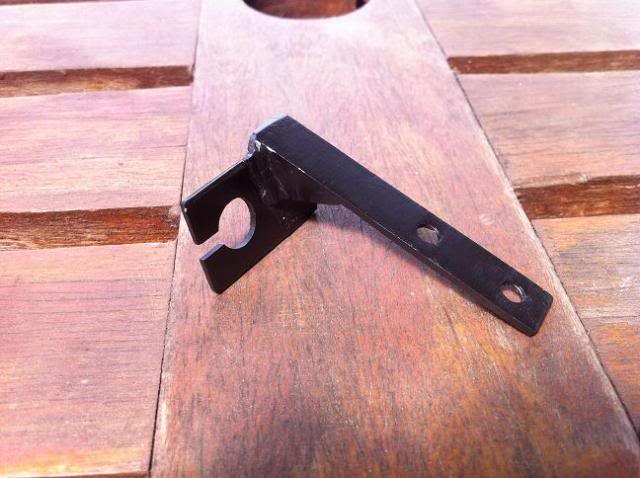
Rover V8 into Gemini conversion
Engine mounts (not finished obviously, need to fully weld and smooth them)
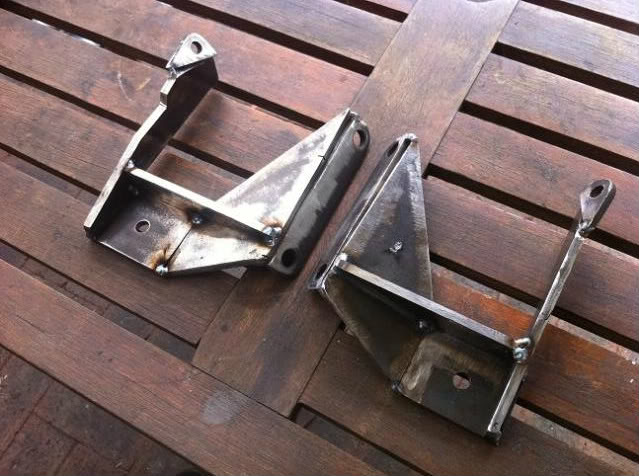
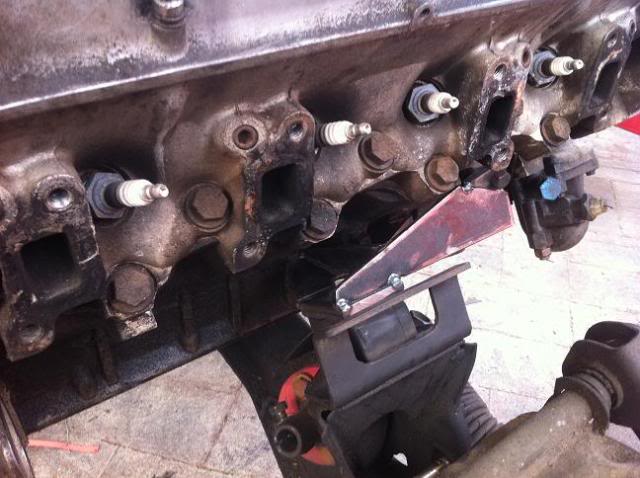
Modified sump
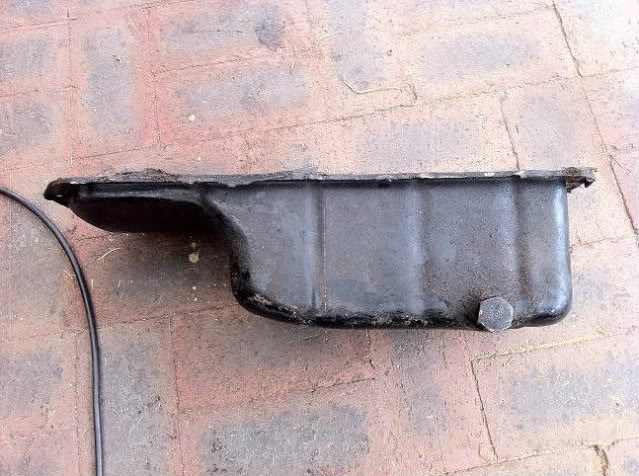
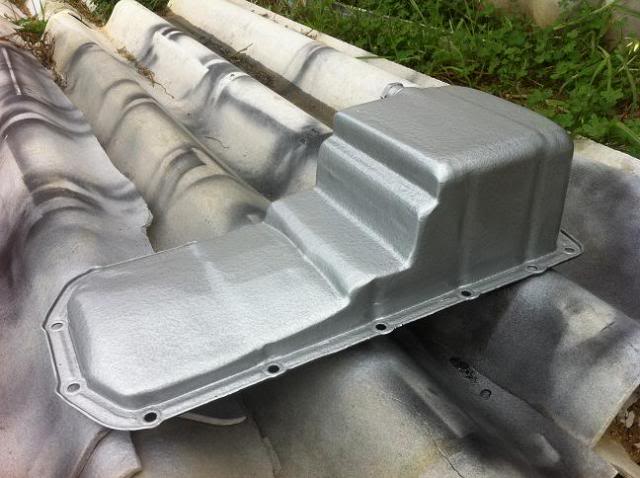
G/box cross-member
The box fouled on the stock mounting position which are welded to the floor so drilled the spot welds out and made it from scratch and used sandwich plates to hold it to the floor
Where it hit.
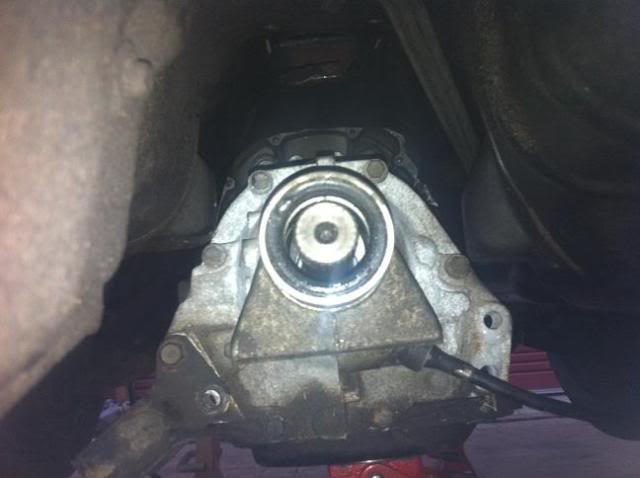
New cross-member beginnings
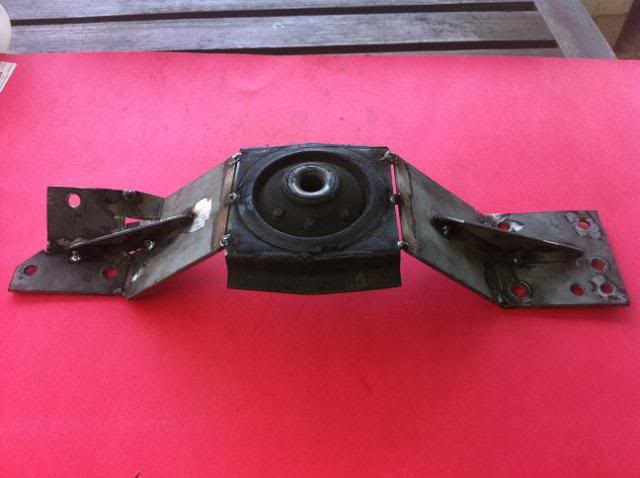
Just about finished, just abit more cleaning up and some paint
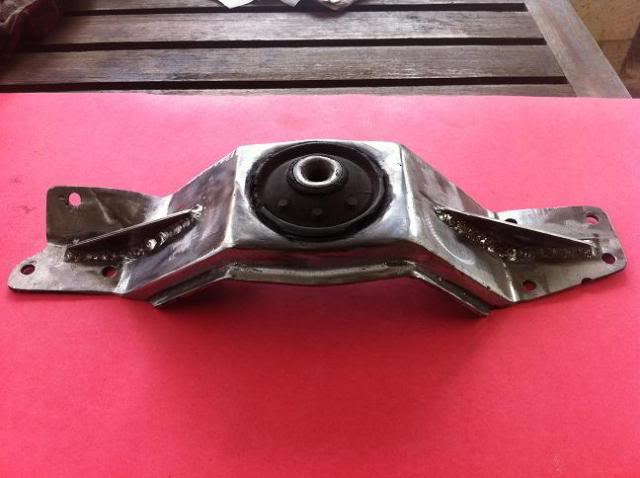
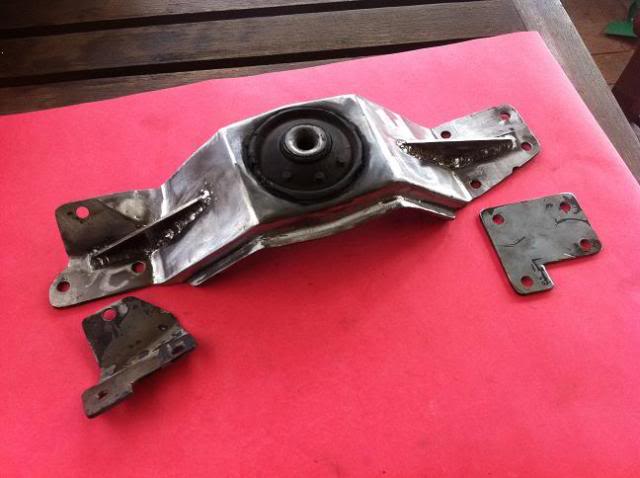
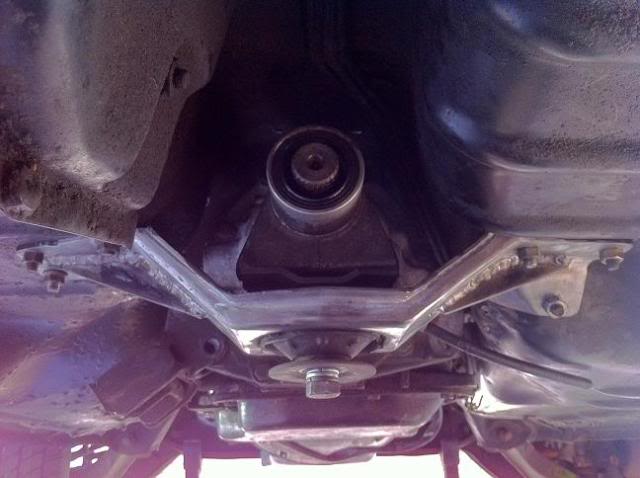

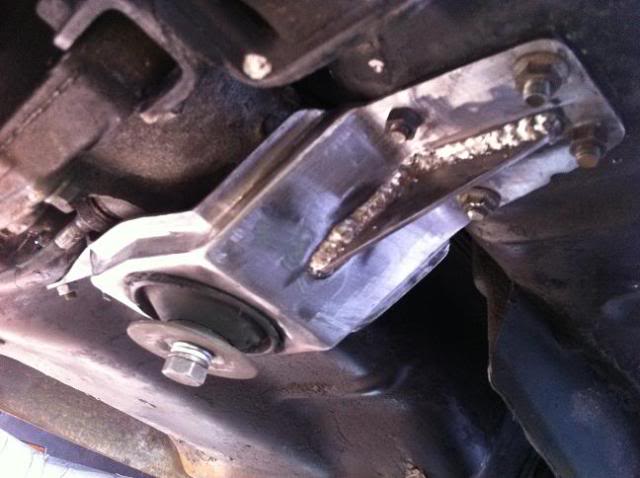