
Welding tips?
#26
Posted 20 May 2008 - 02:45 PM
Tim
#27
Posted 20 May 2008 - 02:50 PM
Pulling a mig will get the weld to pool nice and look good but may not have the penetration for structural strength, especially if you grind and sand your welds.
#28
Posted 20 May 2008 - 02:52 PM

Tim
#29
_1ARC_
Posted 20 May 2008 - 03:46 PM
#30
Posted 20 May 2008 - 04:35 PM
When using "Globular Transfer"(20-23 Volts) then youre in between the two modes and can push or pull.
"Spray Transfer"(>24 Volts) is definately a push (with solid wire and gas)
Disclaimer: Wire Thickness,Gas type, and everything else will play a part.
#31
Posted 20 May 2008 - 05:05 PM
#32
_1ARC_
Posted 20 May 2008 - 05:17 PM
#33
Posted 20 May 2008 - 06:07 PM
You should be in politics.

#34
Posted 20 May 2008 - 06:11 PM
Used to be a Boilermaker/Pipefitter.
#35
Posted 20 May 2008 - 06:37 PM
Like the ones that estimate government projects that "blow out" by a billion or 2 (give or take).
#36
Posted 20 May 2008 - 09:47 PM
Never trust the media mate.

#37
_Big T_
Posted 20 May 2008 - 11:28 PM

Anyway, I checked the gas and although it wasnt really audible through the end of the torch I did manage to poke a hole in my ear with the wire feed

I did as suggested and turned the gas off to see how the weld would work.... it didnt. I ended up with a wire spaghetti mess. So I suppose Im getting gas.
I paid more attention to the tip to work distance and I also cleaned up all my surfaces. I took a bit more time with my weld speed and concentrated on the weld pool instead of the arc.
End result from all of this was better than my last efforts. Im still getting a bit too much wire but its getting better.
Here are a few pics from my efforts tonight.
Me in the traditional Gangsta Welda pose. Dont dis me homies or I'll bust an arc in ya eye !!
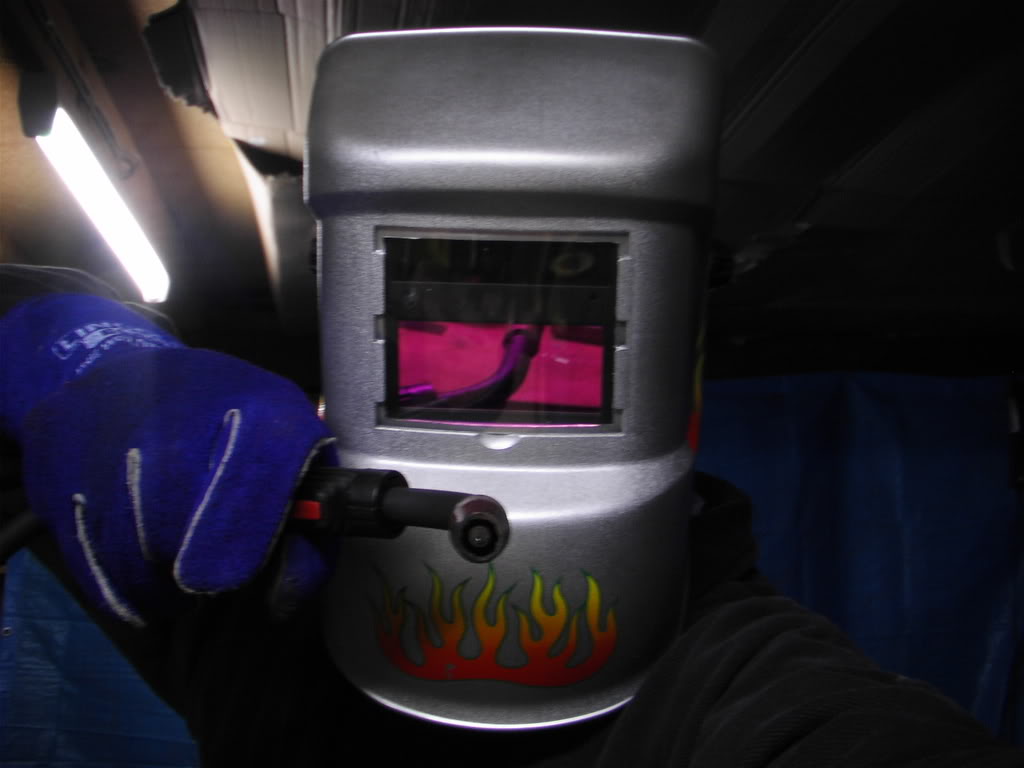
My gat
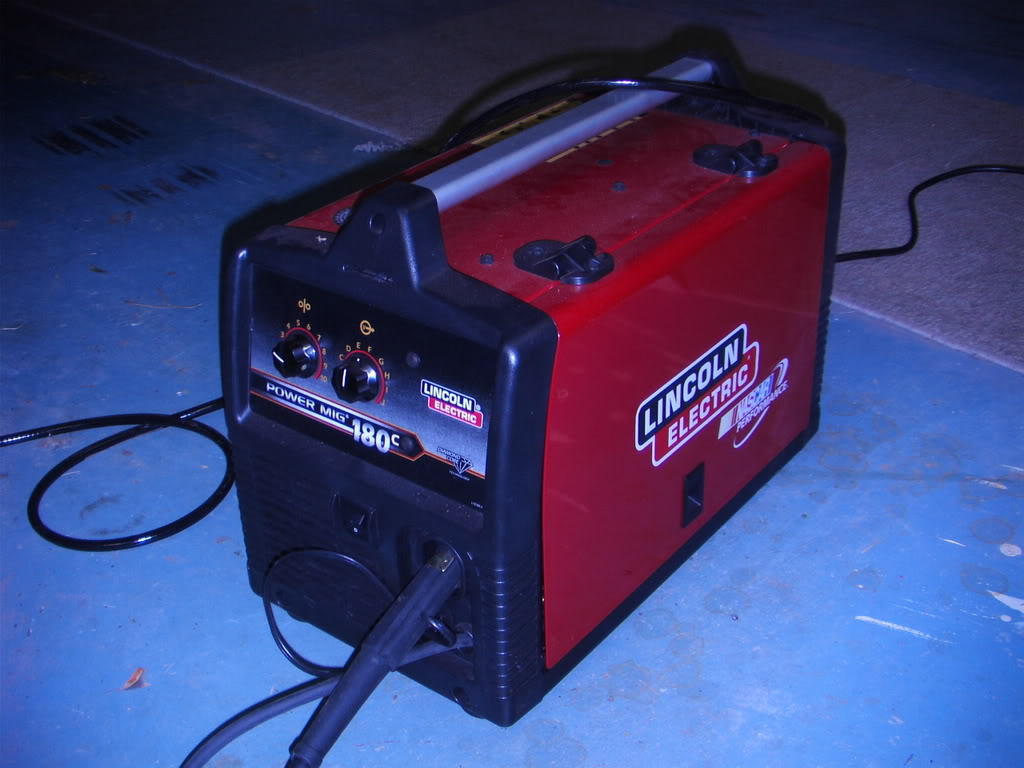
After about 15 mins practice
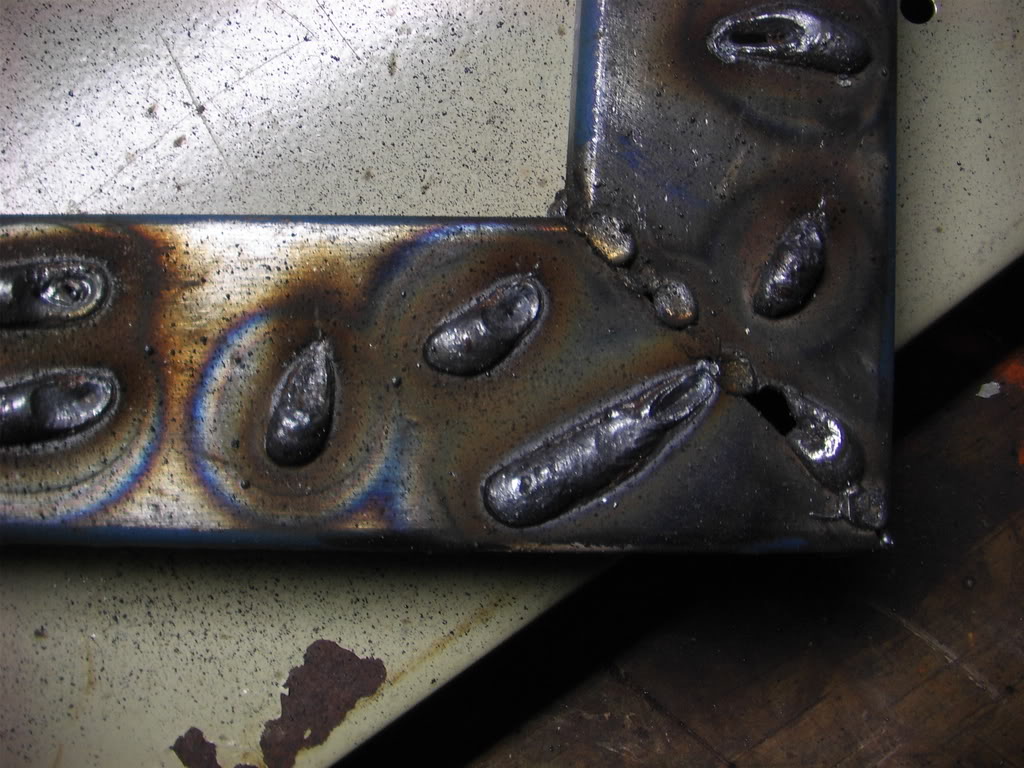
Close up of above. Why does the weld "crater" at the end?
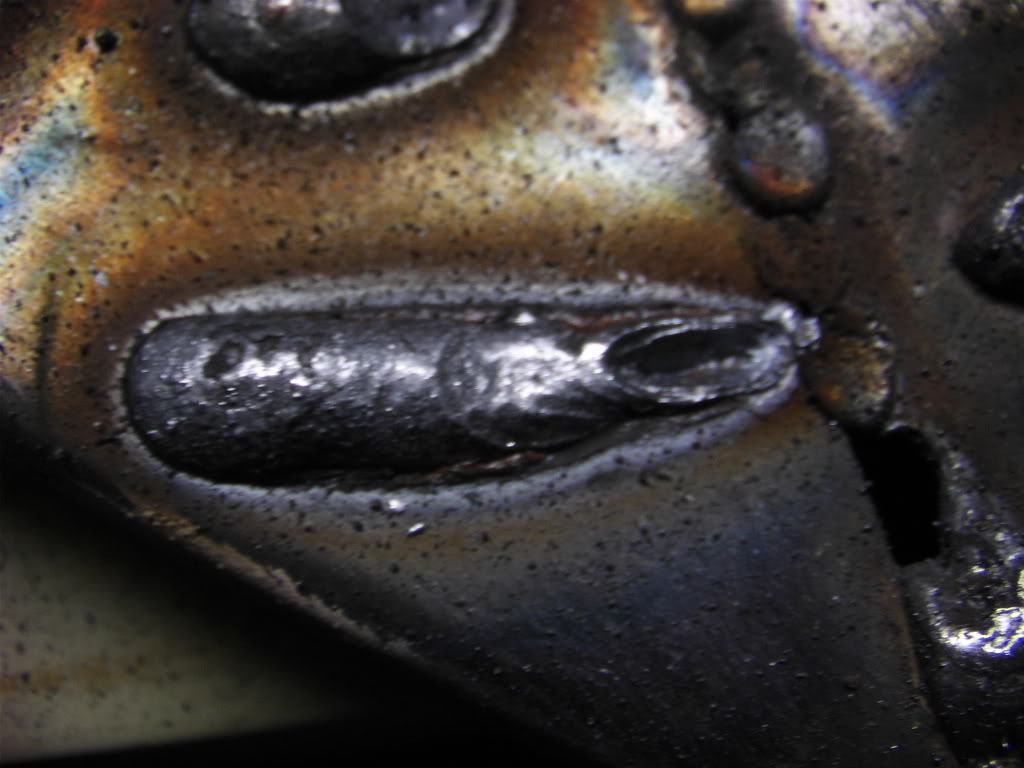
My last three welds. I took a bit more time with these and got decent penetration. I didnt go through the steel but could see where the welds were on the underside.
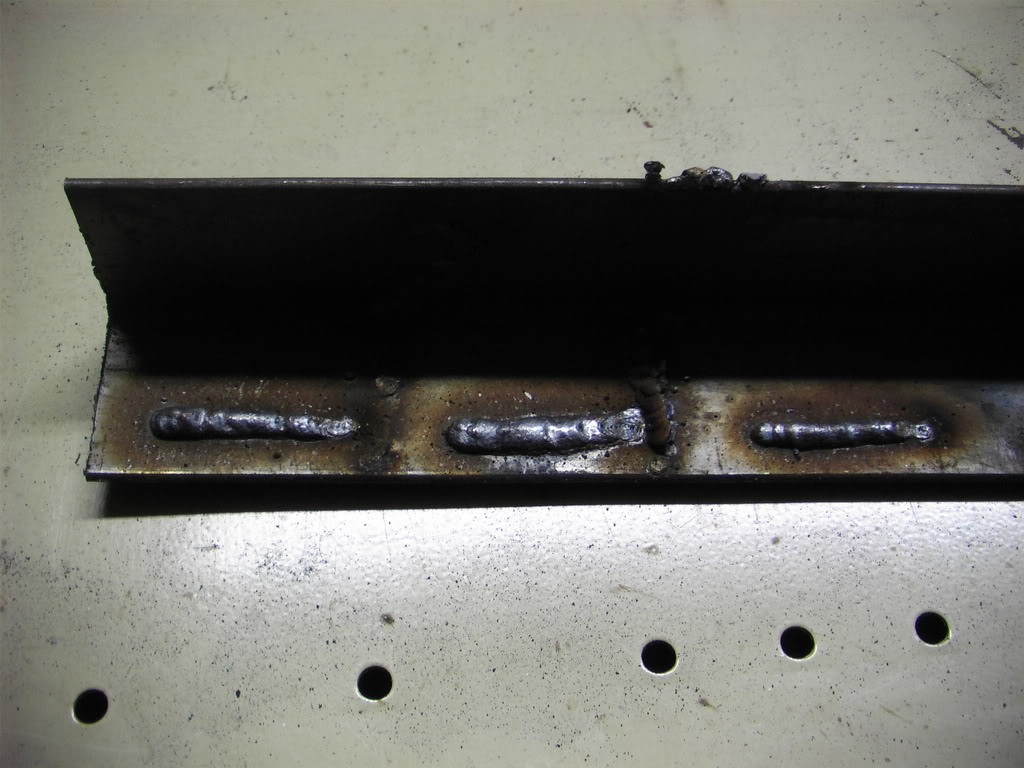
Close up of my last weld. The weld on the right was one of my very first efforts.
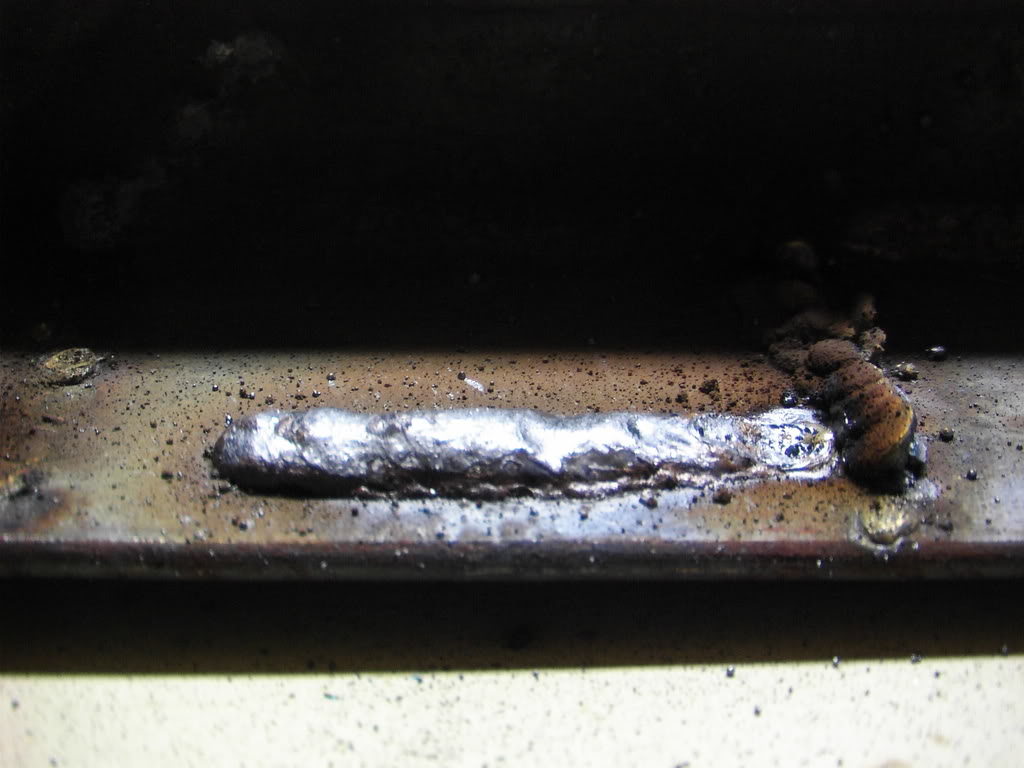
So a couple of Q's.
1.Does it still look like I have a lack of gas issue?
2. How can I avoid the crater effect when I finish my weld?
Still got along way to go but Im feeling a bit more confident than last time.
Cheers fellas,
T
#38
Posted 21 May 2008 - 05:47 AM
For ya crater,
Pause at end of your run and just give the weld a quick dab of wire with out moving , but the less wire will help ya crater also.
#39
_luv the uc_
Posted 21 May 2008 - 05:47 AM
#40
Posted 21 May 2008 - 11:08 AM
Looks like you are getting more confident with technique.
Not long now and you will be welding up exhausts with your arm wedged between a tyre and a wheel arch, and your head stuck up between the diff and the floorpan, in thongs, shorts, and due to the lack of space for the helmet, closing your eyes to avoid the arc!

#41
_SLR_6_
Posted 21 May 2008 - 11:46 AM
#42
Posted 21 May 2008 - 02:01 PM
#43
Posted 21 May 2008 - 02:04 PM
#44
_dandapalm_
Posted 21 May 2008 - 03:24 PM
Check the machine, check the machine, check the machine.
1.Read book on polarity of welder. This is obvious, but should be negative ground.Also note that at different times of day, welder may be getting less than 240 Volts which is very common in some non industrial areas, so just note that at 7pm etc dinner time, welder will drop a cog if you are in one of those areas. SERIOUSLY !!!
2. Check tension on roll of wire and make sure that wire is mounted the right way around so it is pulling wire from bottom of roll "through" the rollers rather than from the top with a lot of effort required. With small rolls, make sure it is not so tight that rollers are slipping as they try to pull wire through. THIS IS IMPORTANT!!!
3. Gas pressure and type. I used to simply use a "hot" gas like Corgon 52 or similar, but with general welding , just about any GP will do the trick. You really must be able to hear the gas from the end of the nozzle, and dont be afraid to wind up the gas until you can hear it OR see the difference in the weld.
4. Listen to the welder and hear the stages of weld develop as with modern machines they have several helpful diodes and solenoid adjustments set at the factory.
Start up is always a bitch with heavy plate or cold steel , so just give up on using RHS and find some scrap plate that will have an even temp after u have done a few welds and not get too much pre heat into it. With thin RHS you will be welding like a star with the base material so hot after a few welds that when you turn around and start on a cold piece, you will be disappointed.
With the welder running on your current setting as you run a small line on a plate , get a mate to start turning up the wire speed while you are welding. It will no doubt start to bounce while you are welding , but at that point yell out and tell him to back off until you can literally see the wire melting just away from the job and be careful not to grab the tip and melt it solid!!!!. Ok these are your two extremes of your welding range, so depending on your welding angle, work in between these extremes and if working with cold plate , just dial in a touch more heat to overcome the start up issue. You will "hear" that sharp crack when it is right and NEVER forget that sound , trust me.....I hear it in my sleep after running a welding shop for 15 years!!
I cannot stress enough that the job has to be clean, once you get established, you will develop techniques to overcome dirty or rusty steel , but initially when trying to develop a style, just keep it very very clean.
I am guessing you are using 0.9 mm wire?? It is easy to run the 0.9mm but I am out of touch with the common small welder situation and what is practical. I hear about ppl using 0.6mm and just think this would be more trouble than its worth with any medium ( non panel work) fabrication.
It also goes without saying that you will become an artist quicker than you think, with a calm start up arc and the ability to really feel the end of the weld and know when to just hold it that fraction of a second before you stop welding.
Looking at all pics, I can see a HUGE improvement mate and this is the only way to improve and you would be excited about the improvements. It is a skill you have for life and I hope what I wrote just gave you some more things to consider.
If I had to set this welder up, I would be really looking at the gas and just make some notes on settings, but remember what I said about building up too much heat in a test piece, so alternate between pieces so you can simulate a cold start and settings that mean something.
But...........good on ya for wanting to learn. I had a fab shop with 5 welding stations and a heap of workers doing repetition work for government departments. We mainly had WIA 325's, 400's and one 600, so we got pretty busy and I had a job on my hands keeping the welding plant in good order !!! I hope this helped and sorry if I overlooked anything in set up of machine.
Am convinced that wire used is a flux filled or super core wire, looking at micro spatter and edges of weld.....but again, my humble opinion... Cheers
Edited by dandapalm, 21 May 2008 - 03:26 PM.
#45
_Big T_
Posted 21 May 2008 - 04:00 PM
Dandapalm you have highlighted some points I didnt even consider, especially the 240 volt one. Fortunately my welder has a trip switch which will activate if the welders current requirements are not met. But I see your point about dinner time

Thanks for the vote of confidence too, it is appreciated.
I cant wait to get home and give the welder a bloody good look over.

Initially I wasnt going to worry about posting my question, I was just going to solder, um, I mean soldier on and see how I went. Im sure glad I did post though.
I will post an update tonight or tomorrow.
Cheers once again,
Big T
#46
_3point3_
Posted 21 May 2008 - 07:32 PM

From my experience power is often a problem.
These things draw heaps of amps when working properley.
Check your welder's specks!
If 10 amps @ 240vac, it means 10 amps!
Out in the garage (longer run) then a "cheap" extension lead you can get less than 7amps. (is the extension lead warm?)
Skill can only be learnt. Keep going.
#47
_Yella SLuR_
Posted 21 May 2008 - 10:14 PM
I've been away for the last 3 days, so apologies for not getting back earlier.
Are you aware that wire speed sets the welding amps (heat)? For more heat, turn up wire speed, and for less turn it down. Also, for a given power settings on the welder, there will only be a narrow band of wire speed that will produce a good weld. Adjust the wire speed (very fine adjustments) till you get the nice sharp cracking sound (good MIG weld sound).
Also, make sure you keep that tip in nice and close. It will spit, fart and carry on if you are too far away. Jam it right in there, and don't be too concerned if you can't see the tip. Look for the right light and sound coming from the welder.
Practice practice. You've got the hole because there is too much heat in the metal. Rectify that particular bit by moving the gun a little bit faster.
Gas. Whle starting you should be at 14 L/s. Once you get better you can drop it back to 12 L/S.
Welding is frustrating. The difference between a good and bad welds is two poofteenths of adjustment to either settings on the machine or technique.
Enjoy. Practice, practice, practice.
EDIT: God, there is always more. Just make sure you are comfortable when you are welding. It's amazing what a difference that can make. I actually use my left arm as a rest.
Also it assists the wire feed if there are no tight twists or bends in the line up to your gun.
There's heaps to learn mate. Keep going.
Edited by Yella SLuR, 21 May 2008 - 10:22 PM.
#48
_Yella SLuR_
Posted 21 May 2008 - 10:24 PM
#49
_Big T_
Posted 21 May 2008 - 10:44 PM
I'VE GOT GAS !!!!

I took heed of the advice posted and checked all my fittings. I re-seated the torch hose connection to the body of the welder and (I think this is the kicker), opened my gas valve fully.
Pulled the trigger on the torch and lo and behold I could feel and hear gas coming out.
I ran a few beads and I admit I didnt clean up the steel before doing so but I was keen to test. The end result was this....
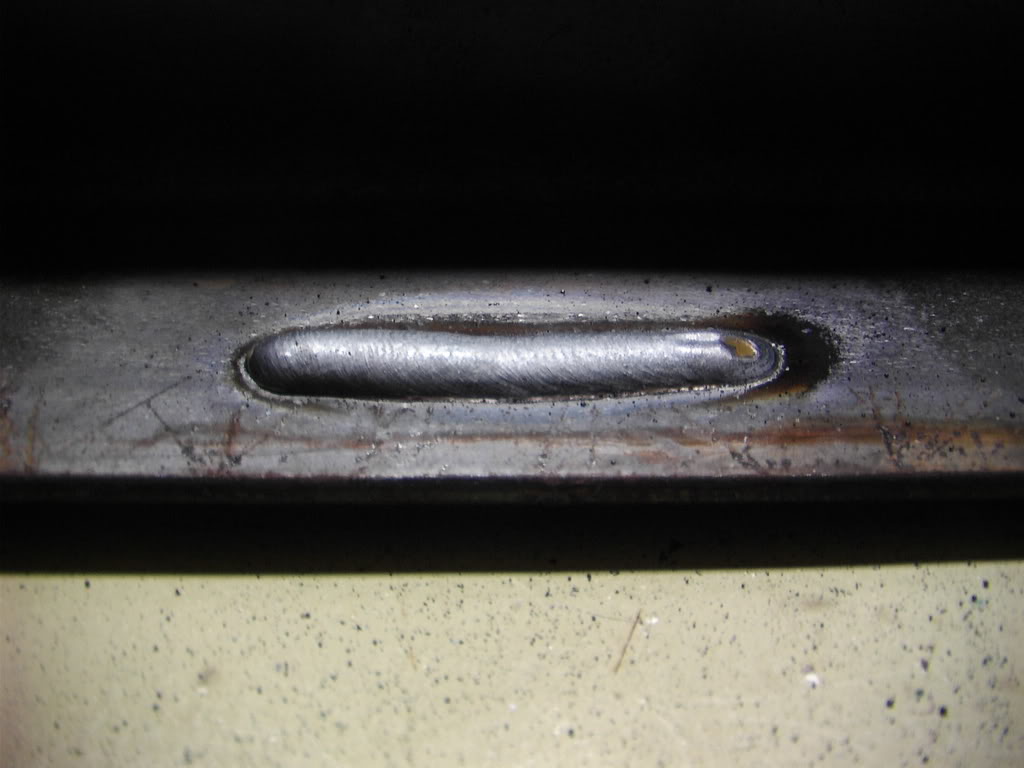
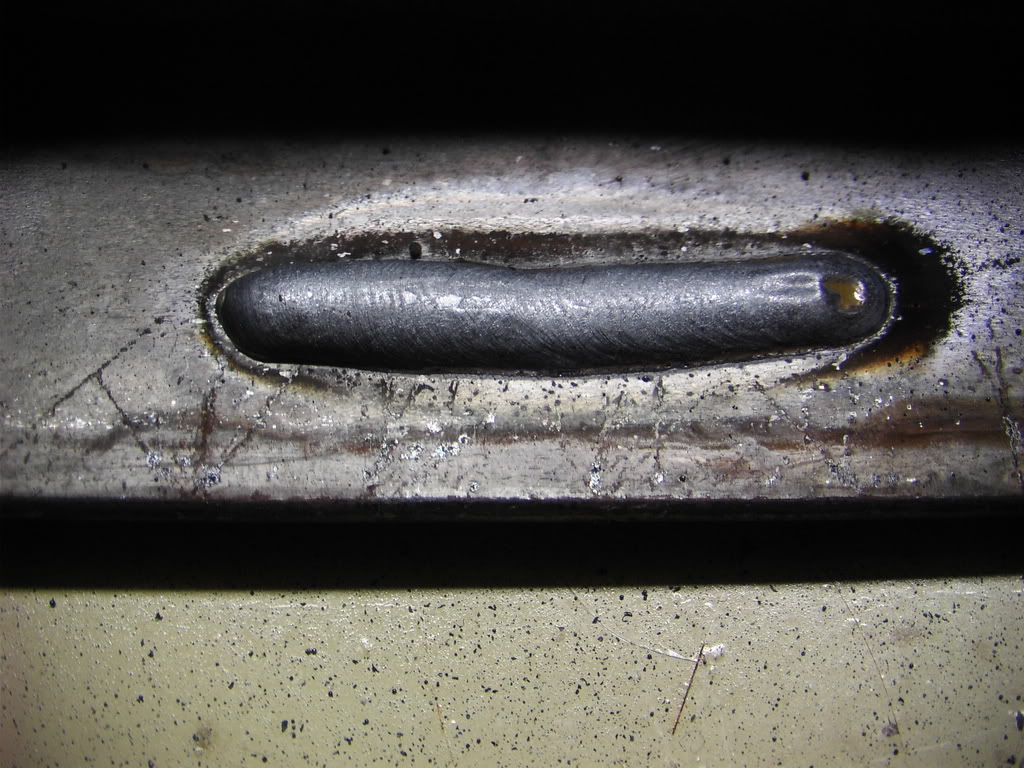
Underside
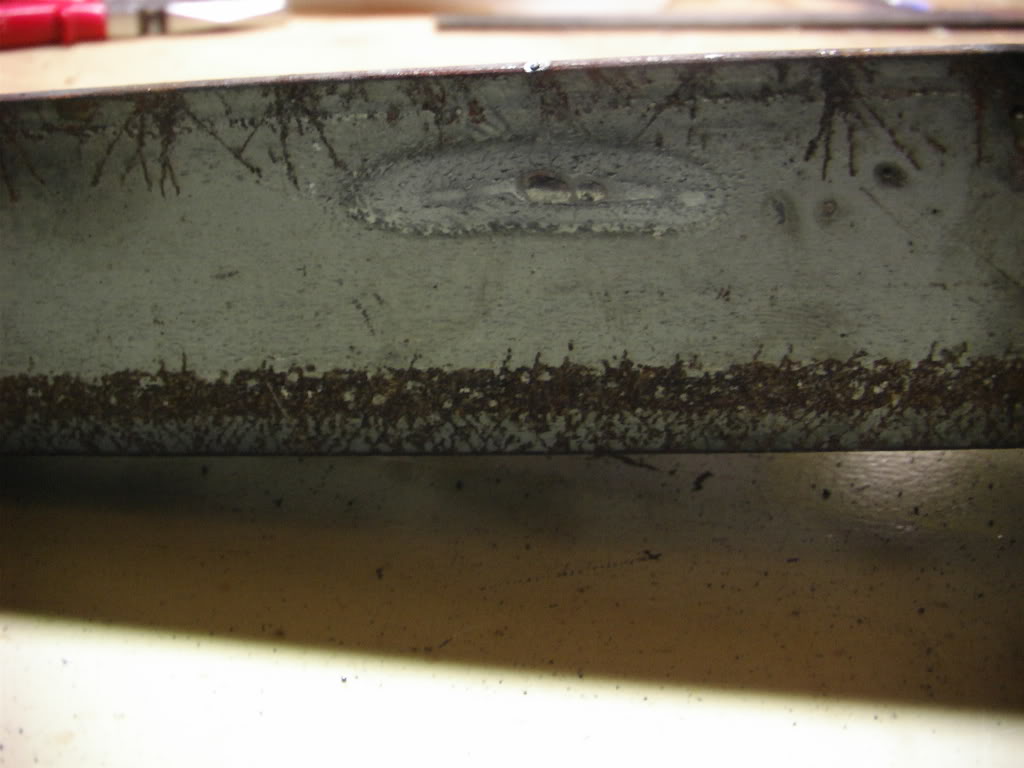
Needless to say I am very happy and oh so appreciative of everybodies help. It is one of those things I wouldnt have picked up on as I didnt know any different.
Now that I have the gas issue sorted I can concentrate on all the other tips given. I'm feeling pretty good about this welding gig right now. I've got heaps to learn but seeing a nice clean bead of steel is cool.
Im going to run around on the weekend and see if I can pick up some thick plate to practice on.
Cheers, and thanks heaps to every one for their input.

T
#50
Posted 21 May 2008 - 11:14 PM




1 user(s) are reading this topic
0 members, 1 guests, 0 anonymous users