
Dirtbags dream car rebuild! HK monaro!
#201
_Gunmetal LH_
Posted 17 May 2011 - 08:59 PM
Here's a silly idea Dirtbag- do the whole car like that...
In aluminium!
Stick it all on a kingswood chassis! You'd have the lightest Monaro yet!
#202
Posted 17 May 2011 - 10:20 PM

#203
_DomDom_
Posted 17 May 2011 - 11:15 PM
That is awesome Tim. That rear quarter looks just like a......quarter.
I'm a builder and I build timber boats so I know wood pretty well but i wish I could do steel like that. I suppose it takes the right tools and the know how to use them correctly.
Thanks for showing us how its done I couldn't have envisaged it otherwise.
Dom
BTW I like this comment "you could make a monaro panel by panel". Good one Neils LX.
#204
_dirtbag_
Posted 17 May 2011 - 11:18 PM
Tim, that is awesome, Kev is going to have an excellent car when you have finished, I told the wife that I want you to do my next car, shit that woman can go on
Oh crap! Do I have to give it back????? That changes everything......
#205
_Kush_
Posted 18 May 2011 - 08:47 AM
You won't be able to get rid of me!

Excellent work, Tim

Rock on!
#206
_nzstato_
Posted 18 May 2011 - 09:09 AM
Looking great as always

#207
_judgelj_
Posted 18 May 2011 - 01:35 PM
wont there be a difference in surface depth or will you be cutting out the existing section and replacing it with the new?
#208
_nzstato_
Posted 18 May 2011 - 01:42 PM
#209
Posted 18 May 2011 - 01:48 PM
#210
_jabba_
Posted 18 May 2011 - 02:52 PM


#211
Posted 18 May 2011 - 03:04 PM
Are you turning it into a Holden?At least its only a ford that im cutting the crap outta!
#212
_jabba_
Posted 18 May 2011 - 08:38 PM
Nice work, thanks for taking the time to post up all the progress pics, its much more interesting seeing this stuff than looking at finished cars.
I completely agree, i love looking at build logs with loads of progress pics so you get an idea on how it was done. The real art on a car like this is the transformation

Are you turning it into a Holden?
Plenty of Holden steel is going into its making

#213
_dirtbag_
Posted 18 May 2011 - 11:13 PM
nzstato, I put the centre swage in with a panbrake, as it's in a straight line. None of the other shapes were straight so used the bead roller.
As for the wheeling, I only wheeled the top half of the panel, so didn't have to roll over the swage. The lower half of the panel I just twisted into shape by hand, as it doesn't have as much crown/curve as the top half.
Well I did a bit more today.
I started on the lower swage and the small section of wheel arch. I also used the bead roller to start the fold where the lower part of the panel folds under behind the wheel arch. I can then hammer and dolly the whole section up from there.

I also wheeled the panel a bit more, and hammered out the flare a bit better. Plus I pulled the lower section into shape by hand. One of the reasons I like using the 1.15 zinc sheet instead of the more popular 1mm cold rolled is the fact it's a lot harder to shape, meaning you can really get into it without going to far with the shaping. Cold rolled sheet is a lot easier to form, but the zinc is stronger and can hold its shape a lot better.
You can see here how far the middle of the panel is in the air, meaning there is a fair bit of shape in the panel now. Yay : )

It's fitting on the car a lot better now. I still need to fold the lower lip up behind the wheel arch.

I used a heavy ball pein hammer and a largish flat dolly to hammer the lower lip up. It has a slight curve and a fairly wide return, so took a bit of convincing.


Starting to look like it belongs there.

I also hammer and dollied the top edge of the new panel so it curled in more towards the body. I'm pretty happy with how it's sitting on there now.

The front of the panel is sitting quite well now too.

I feel like a fraud explaining all this step by step like I know what I'm doing, when I have had no training whatsoever, but for those interested, the tools I used to do this are english wheel, panbrake (folder), bead roller and these assorted hammers and dollies.

This is a bad pic, but it shows the dies I used to make the lower swage.

Well now I'm happy enough with the shape of the new piece, it's time to remove the old piece.
When I traced out the shape I needed, I made the front section longer than it needed to be so I could cut the weld off from where I joined the new front half of the quarter. I didn't want two welds side by side, so this way there will still only be one weld down the panel.
My finger is on the weld I did when I fitted the new front half of the rear quarter.

I traced the new piece onto the car, so i could see where to cut. As I cut it, I left a few bumps of the original metal in the way, so when I hold the new piece up to butt weld on, it has something to lean against, rather than just falling in against the inner panels. Once it's tacked in place I can just run a 1mm cutting discs through it and line the two pieces up for a nice flush butt weld.

Pretty : )

Found a couple of nice things inside.
The lower corner of the wheel arch was all bog. There's a nice big chunk of it inside there too.

I put my finger in the pic so you can see how thick the filler is here.Yes, that;s filler in the spare wheel well. Nice : )

I also spent a bit of time tonight starting to clean up the inner panels. I'll take all this back to bare metal like I did the front half of the quarter and etch prime it before I weld the new outer piece on.

The old and the new : )


Well that's it for today. I had to spend a fair while up at the new house, but tomorrow morning I'll go and pick up all the front end bits from the powder coaters.
#214
_jabba_
Posted 18 May 2011 - 11:22 PM
#215
_nzstato_
Posted 19 May 2011 - 05:44 AM
#216
_dirtbag_
Posted 19 May 2011 - 07:29 AM
#217
_nzstato_
Posted 19 May 2011 - 08:04 AM
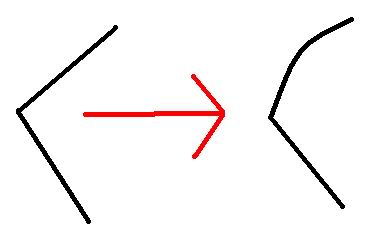
#218
_dirtbag_
Posted 19 May 2011 - 08:17 AM
Just so people understand what Sam is saying, whereever the top and bottom rollers of the english wheel touch the metal, it creates a high spot, so if you roll a panel too much in one spot, you need to roll the rest of the panel to bring it up, you can't roll things down.
#219
_nzstato_
Posted 19 May 2011 - 08:41 AM
#220
_dirtbag_
Posted 19 May 2011 - 08:45 AM
#221
_nzstato_
Posted 19 May 2011 - 09:02 AM
Rod Tempero
#222
_1uzbt1_
Posted 19 May 2011 - 10:53 AM
Just a few question, what brand and where did you get your bead roller from? some where in the states wasn't it?
Also what are those pins you are using to hold the panel onto the old one?
#223
_jabba_
Posted 19 May 2011 - 03:01 PM
#224
_Gunmetal LH_
Posted 19 May 2011 - 03:13 PM

#225
Posted 19 May 2011 - 05:23 PM
Not to many people around that have the skills to attempt what you are doing here.
keep up the good work
0 user(s) are reading this topic
0 members, 0 guests, 0 anonymous users