I just need a spare block, I have the time.
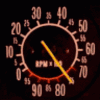
'HOLDEN FLAT or V12'
#51
Posted 27 June 2013 - 09:51 PM
#52
Posted 27 June 2013 - 09:58 PM
Good Man Vick,
You will need 2 identical cams as we all know, so what spec should they be?
I just need a spare block, I have the time.
#53
_STRAIGHTLINEMICK_
Posted 27 June 2013 - 10:20 PM
I have plenty of blocks , leave cam specs to me
#54
Posted 27 June 2013 - 10:30 PM
Anyone remember those weird Rover engines (K something I think) that had the head attached with through bolts that screwed into the main caps?
Freelander 4cyl? Undo the rocker cover and the sump falls off from memory?
#55
Posted 27 June 2013 - 10:36 PM
OK Mick,
Now the timing, we could use two 6cyl distributors ( one for each cam ) firing 180 degrees apart - is that correct?
also we would reverse a block and make the cam drive from the other end.
p.s. exhaust can still come from the top using Holden 6 heads and a tunnel tube ram central carby system
I have plenty of blocks , leave cam specs to me
#56
Posted 28 June 2013 - 06:57 AM
If there are no more issues then somebody needs to build this thing
All jokes aside it would make a really cool coffee table, I'm sure it wouldn't be hard to spin a good story that would fool most people
#57
Posted 28 June 2013 - 07:23 AM
All jokes aside it would make a really cool coffee table, I'm sure it wouldn't be hard to spin a good story that would fool most people
Now you got me thinking.
#58
_Bomber Watson_
Posted 28 June 2013 - 01:34 PM
But wouldnt we have the inlet on top on one side and underneath on the other? Suppose we can run a long mani around for the baby cam side, longer runners will work better for the torque....
#59
Posted 28 June 2013 - 03:34 PM
Just turn the head around...
#60
_STRAIGHTLINEMICK_
Posted 28 June 2013 - 08:04 PM
OK Mick,
Now the timing, we could use two 6cyl distributors ( one for each cam ) firing 180 degrees apart - is that correct?
also we would reverse a block and make the cam drive from the other end.
p.s. exhaust can still come from the top using Holden 6 heads and a tunnel tube ram central carby system
This shit is keeping me awake at night ,the funny and scary thing is we havnt come across a problem big enough to kill the idea .Ok two dizzys on the 1st prototype firing 180deg apart .Both blocks to the front to keep accessories and cam drive where they should be . Heads also stay in the normal position .Cams can be played with later . I like the coffee table idea too .
#61
_Bomber Watson_
Posted 28 June 2013 - 08:13 PM
#62
Posted 28 June 2013 - 11:19 PM
Electric water pump/s, offset blocks by 1/2 inch for con-rod to bores alignment
#63
_STRAIGHTLINEMICK_
Posted 28 June 2013 - 11:27 PM
Yep but you would have to make the fuel bowls vertical or use an efi manifold on the upside down head and hang some su's off it .
Solved the one head up one down problem, get some tomas tripple strom manis and hang su's off them. Three above three below.
#64
_STRAIGHTLINEMICK_
Posted 28 June 2013 - 11:35 PM
Electric water pump/s, offset blocks by 1/2 inch for con-rod to bores alignment
yep or use offset conrods as in a 1275 mini .Dont tell anyone but i have modified 1275 rods in my fj engine .That was to test the stroker combo before I had the H beams made and it's still running now .We could use 2 long rod strokers now we have 436ci
#65
Posted 28 June 2013 - 11:44 PM
Now we are talking Mick,
or a Fraud Crank - 470ci
yep or use offset conrods as in a 1275 mini .Dont tell anyone but i have modified 1275 rods in my fj engine .That was to test the stroker combo before I had the H beams made and it's still running now .We could use 2 long rod strokers now we have 436ci
#66
_Bomber Watson_
Posted 28 June 2013 - 11:49 PM
Yep but you would have to make the fuel bowls vertical or use an efi manifold on the upside down head and hang some su's off it .
Hense i said tomas triple strom mani, ie downdraught, when engine is on its side the carbs are the right way.
#67
_oldjohnno_
Posted 29 June 2013 - 08:07 AM
I dunno if you blokes are serious about this or not, but if you are there are a quite a few things to sort out yet.
Firstly, offsetting the blocks or having one block reversed would be difficult if not impossible. Remember that both blocks have to align with the main journals and that there is a thrust bearing at the back. Not only that, but if you plan to hold it all together with through-bolts then the holes will have to line up. Keeping the blocks aligned would also simplify the cam drives.
While we're on through-bolts; the main bearing oil feed holes pass under the main bolt holes. So if you are going to use through bolts the oil supply for one of the blocks will be blocked off. Probably wouldn't matter though; the feed from the other side would be sufficient though you'd want grooved bearing on both sides.
You'd have to machine about 1/8" (the depth of the cap register) from the bottom of both blocks. Not really a problem but it would make the pan rail very very thin. I haven't checked to see how they would match up but there certainly wouldn't be enough meat to allow a thin adaptor plate. You wouldn't even want to use a gasket here as it would further reduce the rail thickness. A potential show-stopper that needs to be checked. Even if it is workable I think a good rattle could crack the rails off.
Next, how are you going to positively locate the two sides of the main tunnel. As stock the cap fits into a shallow register in the block. It'd be easy to dowel the pan rails but seeing as the skirt on a 202 block is about as stiff as a sheet of paper that's not going to do anything. You could dowel the webs (it'd be a pain in the arse to do but it's possible) and then align bore the main tunnel. If there's enough meat there you may be able to use hollow dowels around the bolts. Either way you'd need a fixture to locate the holes in each block and then align bore afterwards.
What are you going to do with the big-ends? There's no way that 1/2" wide bearings are going to cope with any load, and even if they could you'd have to oil it somehow. And at any rate the big end of the rod and the cap would be so weak and flimsy (remember it has bolts passing thru) to be useless. Another problem would be assembly - how are you going to torque up the second set of bolts? Remember that you can't slide the pistons in from the bottom cos of the main webs. The only solution I can think of would be a master/slave rod arrangement similar to those in a radial aircraft engine. Basically the master rod would be "normal" apart from having a pair of lugs on the cap. The slave rod (think of a rod with two little-ends) would be pinned to these lugs. This way your blocks stay aligned, you keep a full width bearing and you'd be able to assemble it, though it'd still be awkward.
Next, where are you going to collect the oil from? Obviously you'd have to go dry sump, but with no actual sump under the crank how do you scavenge the oil? I don't have any ideas for this one and unless someone comes up with a solution it could be a show-stopper.
I think if you could manage the structural problems the rest would be easy. And I can't help thinking of that big flat area on top of the engine, and how it'd look so much better with a 6:71 sitting on it.
Edited by oldjohnno, 29 June 2013 - 08:11 AM.
#68
_STRAIGHTLINEMICK_
Posted 29 June 2013 - 11:45 AM
I dunno if you blokes are serious about this or not, but if you are there are a quite a few things to sort out yet.
Firstly, offsetting the blocks or having one block reversed would be difficult if not impossible. Remember that both blocks have to align with the main journals and that there is a thrust bearing at the back. Not only that, but if you plan to hold it all together with through-bolts then the holes will have to line up. Keeping the blocks aligned would also simplify the cam drives.
While we're on through-bolts; the main bearing oil feed holes pass under the main bolt holes. So if you are going to use through bolts the oil supply for one of the blocks will be blocked off. Probably wouldn't matter though; the feed from the other side would be sufficient though you'd want grooved bearing on both sides.
You'd have to machine about 1/8" (the depth of the cap register) from the bottom of both blocks. Not really a problem but it would make the pan rail very very thin. I haven't checked to see how they would match up but there certainly wouldn't be enough meat to allow a thin adaptor plate. You wouldn't even want to use a gasket here as it would further reduce the rail thickness. A potential show-stopper that needs to be checked. Even if it is workable I think a good rattle could crack the rails off.
Next, how are you going to positively locate the two sides of the main tunnel. As stock the cap fits into a shallow register in the block. It'd be easy to dowel the pan rails but seeing as the skirt on a 202 block is about as stiff as a sheet of paper that's not going to do anything. You could dowel the webs (it'd be a pain in the arse to do but it's possible) and then align bore the main tunnel. If there's enough meat there you may be able to use hollow dowels around the bolts. Either way you'd need a fixture to locate the holes in each block and then align bore afterwards.
What are you going to do with the big-ends? There's no way that 1/2" wide bearings are going to cope with any load, and even if they could you'd have to oil it somehow. And at any rate the big end of the rod and the cap would be so weak and flimsy (remember it has bolts passing thru) to be useless. Another problem would be assembly - how are you going to torque up the second set of bolts? Remember that you can't slide the pistons in from the bottom cos of the main webs. The only solution I can think of would be a master/slave rod arrangement similar to those in a radial aircraft engine. Basically the master rod would be "normal" apart from having a pair of lugs on the cap. The slave rod (think of a rod with two little-ends) would be pinned to these lugs. This way your blocks stay aligned, you keep a full width bearing and you'd be able to assemble it, though it'd still be awkward.
Next, where are you going to collect the oil from? Obviously you'd have to go dry sump, but with no actual sump under the crank how do you scavenge the oil? I don't have any ideas for this one and unless someone comes up with a solution it could be a show-stopper.
I think if you could manage the structural problems the rest would be easy. And I can't help thinking of that big flat area on top of the engine, and how it'd look so much better with a 6:71 sitting on it.
Were bouncing ideas around here Johhno .I work in engineering in the Defence industry , we need to be positive .look at what can be done .If i had listened to the doubters the narrowed conrods ,reversed and narrowed bearings ,bushed falcon pistons ,1.750" offset ground crankpins in my engine would never have happened.Now i am not saying that this is a practical project but its fun to discuss.If you look at how wide you can make the crankpins and that subaru EA81 bearings are .537" wide then another problem is solved .The blocks would have to stay aligned ,dowelled ,mahined and tunnel bored . If a suitable conrod cant be modified then a custom offset rod can be designed .A spacer can be made to fill the cap registers.
#69
Posted 29 June 2013 - 01:20 PM
Great Minds Oldjohnno and Mick,
Do you think using the main caps as they are and remove material from the other block to allow the main caps to clear on assembly would cause weakness in the casting?
Also if the through bolts did or did not line up, use a bigger main cap to allow for 2 extra tapped holes for the through bolts to connect too. Dave I
#70
_Bomber Watson_
Posted 29 June 2013 - 01:32 PM
#71
Posted 29 June 2013 - 01:45 PM
Nice idea DJ,
Have a look at harley rods :-)
#72
_oldjohnno_
Posted 29 June 2013 - 02:19 PM
Have a look at harley rods :-)
That's fine for a built-up crank, but how are you gonna do that with a one-piece crank?
#73
_oldjohnno_
Posted 29 June 2013 - 02:33 PM
Were bouncing ideas around here Johhno .I work in engineering in the Defence industry , we need to be positive .look at what can be done .If i had listened to the doubters the narrowed conrods ,reversed and narrowed bearings ,bushed falcon pistons ,1.750" offset ground crankpins in my engine would never have happened.Now i am not saying that this is a practical project but its fun to discuss.If you look at how wide you can make the crankpins and that subaru EA81 bearings are .537" wide then another problem is solved .The blocks would have to stay aligned ,dowelled ,mahined and tunnel bored . If a suitable conrod cant be modified then a custom offset rod can be designed .A spacer can be made to fill the cap registers.
Mate I'm not trying to be a party pooper, just trying to be realistic. And it is a fun topic to talk about even if it never gets built. I get that the Subby survived with those tiny bearings, but it only had one piston and rod to deal with and even then the stroke was only about 2-5/8". I havent done the sums but I'd imagine our flat 12 would have loadings of at least four times as much, and that's without a lot of revs. I just cant see them working.
Putting a spacer in the cap registers would be easy but then the main tunnel wouldn't be round. You could get round this by using small journal (186) blocks and line boring them to take a 202 crank but that just creates more problems because now the crank centreline has shifted. So now the cam gears wouldn't mesh properly and the flywheel wouldn't be central in the bellhousing.
As I said, I'm not intentionally being negative and I'm sure it can be built, but I think there's a fair bit to work out yet.
#74
_hutch_
Posted 29 June 2013 - 03:54 PM
I cant get me head around how are ya gunna time the valves,coz arnt the paired pistons gunna be on different strokes ? and is it be a 90 degree "V" or 60 ign isn't going to be a problem that's only a matter of shifting plugleads.
Have seen some strange engines in my time including a CCW 351 fraud in twin engined boat, apparently there is a special cam available so you might be able to get one built
#75
_STRAIGHTLINEMICK_
Posted 29 June 2013 - 03:56 PM
Mate I'm not trying to be a party pooper, just trying to be realistic. And it is a fun topic to talk about even if it never gets built. I get that the Subby survived with those tiny bearings, but it only had one piston and rod to deal with and even then the stroke was only about 2-5/8". I havent done the sums but I'd imagine our flat 12 would have loadings of at least four times as much, and that's without a lot of revs. I just cant see them working.
Putting a spacer in the cap registers would be easy but then the main tunnel wouldn't be round. You could get round this by using small journal (186) blocks and line boring them to take a 202 crank but that just creates more problems because now the crank centreline has shifted. So now the cam gears wouldn't mesh properly and the flywheel wouldn't be central in the bellhousing.
As I said, I'm not intentionally being negative and I'm sure it can be built, but I think there's a fair bit to work out yet.
Thanks Johnno, just ran out to the garage and looked at a block ,youre right you would have to machine all of the register down and tunnel bore after a suitable block alignment and clamping arrangement is nutted out .(could weld lugs to the block and bolt as well as through bolts ) Can somebody look at a big bike crankcase ?Clearances can be machined into the webs to allow the second block to slide over the assembled pistons and rods .Some 2 stroke outboards assemble this way, I think the 1/2" rod bearings will do the job if the oiling is up to it . I have seen a 1.625 " crankpin offset stroker .Even i had my doubts about that one , but i trusted the old boys and that motor made 260rwhp in a torana circuit car ..Small bearings need less oil and are good as long as they don't overheat . Oh yeah i have also seen one with all the counter weights machined off ,apparently it revved like an 1100cc bike but broke the block , after that disaster the minimum counterweight limit was found .
1 user(s) are reading this topic
0 members, 1 guests, 0 anonymous users