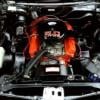
Flywheel bolts
#1
Posted 13 July 2012 - 08:50 PM
#2
_Bomber Watson_
Posted 13 July 2012 - 08:51 PM
Cheers.
#3
_ljxu1torana_
Posted 13 July 2012 - 10:31 PM
defently use loctite on the flywheel bolts.Would it be suggested that I Loctite these bolts and torque to spec? Or is that a bad idea???
#4
Posted 13 July 2012 - 10:56 PM
#5
Posted 14 July 2012 - 08:03 AM
#6
_PeteXU1_
Posted 14 July 2012 - 07:36 PM
#7
_Yella Fella_
Posted 14 July 2012 - 07:55 PM
#8
_PeteXU1_
Posted 14 July 2012 - 09:27 PM
bolts every time?
#9
_ljxu1torana_
Posted 14 July 2012 - 10:04 PM
why did you tighten up the flywheel bolts then took them out,then put loctite on them.it does not make any sense to me.I torque all the bolts up to spec then back them out one by one and loctite them.
#10
_PeteXU1_
Posted 14 July 2012 - 10:23 PM
When I say one by one, I mean after they are all tight, only take out one at a time to apply loctite and re-torque.
Can't remember where I learnt this from...
Edited by PeteXU1, 14 July 2012 - 10:26 PM.
#11
Posted 14 July 2012 - 10:53 PM
http://www.gmh-toran...knocking-noise/
Edited by rodomo, 14 July 2012 - 10:55 PM.
#12
Posted 14 July 2012 - 10:59 PM
#13
Posted 15 July 2012 - 06:30 PM
#14
Posted 15 July 2012 - 08:13 PM
It is common for OEM manuals to state that the reuse of bolts is not permitted, particularly when bonding, sealant or lubricant type products are used in the assembly process.
#15
_PeteXU1_
Posted 16 July 2012 - 05:20 PM
I was using the BMC bolts when my flywheel came loose.
#16
Posted 16 July 2012 - 06:19 PM
As an example, It's a bit tough with the old Holden 6 to use new bolts every time anyway.. They are not available new and whilst the ARP bolts to suit BMC fit, they are near useless - have you seen how small the head clamping area is on the bolt?
I was using the BMC bolts when my flywheel came loose.
drill the crank flange to 7/16 unf, and use '351 Nascar' ARP bolts, direct fit, no shortening and cost $25-30 bucks to replace them.
#17
_Bomber Watson_
Posted 16 July 2012 - 06:45 PM
Cheers.
#18
_tryhard_
Posted 16 July 2012 - 07:00 PM
#19
_Mint_
Posted 16 July 2012 - 07:16 PM
#20
_PeteXU1_
Posted 16 July 2012 - 07:36 PM
drill the crank flange to 7/16 unf, and use '351 Nascar' ARP bolts, direct fit, no shortening and cost $25-30 bucks to replace them.
Done, done and done, although I'm still not convinced new bolts are needed every single time. How many times have the standard bolts been used, reused and reused again ? At $30, though, they are cheap enough for piece of mind.
#21
Posted 16 July 2012 - 07:53 PM
I looked at that, doesnt look like it would leave much material around the ooutside of the flange??
Cheers.
still shitloads mate.
the crank in my car has 2 flywheel holes HELICOILED to 7/16.
some numpty stripped a thread and retapped it in a witworth thread
flywheel has never loosened on my car.
#22
_Bomber Watson_
Posted 16 July 2012 - 07:56 PM
I assume i'll get shouted at using a hand drill and tap

Cheers.
#23
Posted 17 July 2012 - 09:43 AM
There is a difference between a good condition bolt and a poor condition bolt.
Get a thread gauge and measure the threads stretch. If the bolt it overly stretched, turf it.
If the bolts all measure up OK (i.e. very little stretch) then I say re-use them.
I'm running standard flywheel bolts on explosion proof flywheels in both my orange LJ and the purple track car (both spun 6000+)
The ARP bolts that suit standard threads are useless. They may have an excellent resistance, but the heads just dont have the surface area to ensure they "lock" when done up IMO.
#24
Posted 17 July 2012 - 09:50 AM
#25
_Ken_
Posted 17 July 2012 - 10:27 AM
1 user(s) are reading this topic
0 members, 1 guests, 0 anonymous users